随着科学技术的不断发展,当前的工业自动化也发生了很大的变革,传统的依靠继电器和电子线路来实现的系统控制已经不能满足系统的控制要求,尤其在石化行业,无论对控制系统的带点能力还是数据存储及运算能力、可靠性等指标都有了更高的要求。
在石油化工企业中,为了配合生产流程,要对原材料、半成品、成品等进行运输和存储,因此企业均建有大量的各类存储罐,罐区储罐参数的精确检测、工艺流程的有效管理,对于相关生产装置的安全和平稳运行具有十分重要的意义,前期多数用户采用人工检测的方式管理整个灌区,导致管理工作量大且易发生危险,为此本文提出了以和利时LK PLC为下位的控制系统和上位采用HollyView进行组态的罐区控制系统设计思路,通过此系统的应用大大提高了控制过程中的稳定性、可靠性,从而实现整个系统运营的经济、合理和高效。
2灌区系统工艺
此系统主要控制三个灌区分别是北罐区、南罐区、旧罐区,每个罐区都对应不同的泵和阀门,罐区内装车都有计量系统,当计量流量发出到达信号时相对应的阀门和泵关闭,同时当每个罐区内液位、温度出现低报警、低低报警、高报警、高高报警时进行相应的连锁动作。
所有泵、阀门的启停及状态均可在上位机进行操作与显示,报警信息及趋势图也可以根据时间进行查询,实时显示温度、流量、液位等数据,另外每个阀门在手动状态下均可单独进行控制,方便操作人员进行检修。北灌区的工艺流程图如图1所示。
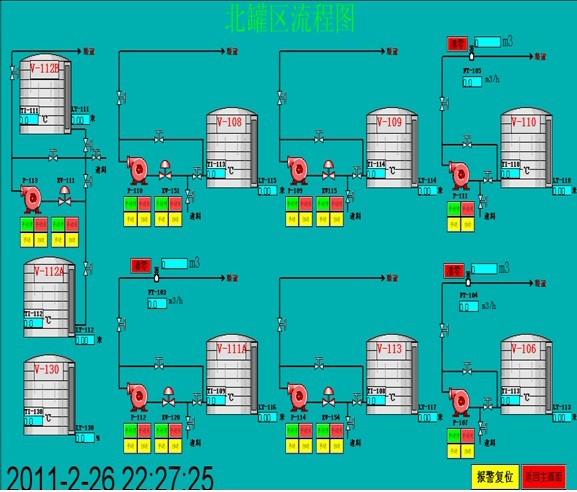
图1 北罐区流程图
3系统设计
系统主要以北京和利时公司LK系列PLC为核心、执行机构、声控报警、仪表系统等组成,主要控制26个不同储罐的温度、液位、流量等,还包括13台泵及9台开关阀的控制,所有储罐均设置液位高低限报警、温度报警、流量控制。在中央控制室设置操作员站和工程师站,并联网至总控室,方便人员对整厂的系统监控与管理,硬件结构示意图如图2所示。
共0条 [查看全部] 网友评论