一、问题提出
目前,国内年产单体40万吨及以上合成氨装置设计中,合成气压缩机、氨气压缩机、二氧化碳压缩机等主压缩机组主要采用“锅炉+汽轮机驱动”的方式生产运行。该种陈旧的建设模式,在新的经济形式和节能减排的国家背景下,存在以下几方面的问题:
1、在新建项目中,“锅炉+汽轮机驱动”的方式投资高、占地面积大、建设周期长。
2、装置投产后,燃煤锅炉的运营维护成本高。
3、燃煤锅炉能效低,厂区蒸汽跑、冒严重、烟气排放环境污染严重。
4、系统调节性能差,生产效率低,能源浪费较大。
5、锅炉蒸汽生产水耗、煤耗指标高,生产成本压力大。
综合上述因素,结合目前国内超大功率高压变频传动技术的成熟应用。该项目在设计中考虑采用电力驱动替代“锅炉+汽轮机驱动”。
二、经济性可行性分析
采用电力驱动系统,将直接节约锅炉占地、建设投入,以及后续运营维护成本和环境污染,提供生产效率。针对两种驱动方式的经济性比较如下表1所示。
表1 合成氨装置主机系统两种不同驱动方式的经济性比较
序号
|
项目分项
|
汽轮机驱动
|
电气驱动
|
指标差值
|
1
|
设备构成
|
锅炉+汽轮机
|
电气+变频器
|
|
2
|
占地面积
|
8900m2
|
300 m2
|
减少98.5%
|
3
|
项目投资
|
12800万元
|
4100万元
|
节约68.0%
|
4
|
建设周期
|
16个月
|
5个月
|
缩短68.8%
|
5
|
生产运营
|
0.43元/kWh
|
0.40元/kWh
|
降低0.03元/kWh
|
6
|
水资源消耗
|
30g/kWh
|
—
|
节约30g/kWh
|
7
|
煤资源消耗
|
392g/kWh
|
320g/kWh
|
节约72g/kWh
|
8
|
环境污染源
|
蒸汽、热、SO2、烟气
|
无
|
环保
|
从上述两种方式的比对分析看,电气驱动在经济性上优势明显。不仅可以节约项目投资费用、建设周期,获得显著的企业收益;而且能够取得良好的社会效益。采用该节能、环保、高效的新型结构模式,符合企业新型发展模式,节能减排、可持续发展政策。
三、技术可行性分析
该40万吨合成氨装置的三台主辅机设备分别为:18MW合成气压缩机、11MW氨气压缩机、11.5MW二氧化碳压缩机。根据工艺生产对设备工况的需求,结合电气驱动的需要。电气驱动系统主要需具备以下几方面的能力:
1.采用高压电动机驱动,通过增速齿轮箱满足压缩机系统的高速运行需要。
2.能够依工艺需求,进行分阶段加减速调节控制;满足系统逐步升温、升压。
3.能够根据合成氨装置的整体生产需求进行压缩机转速、气量调节。
4.压缩机采取软启动、软停车方式,对电网和压缩机机械系统冲击负荷小于额定的2.5倍转矩;能够承受压缩机喘振产生的1.5 Tn波动负荷。
5.电气系统对电网无冲击,网侧功率因数大于0.9、对电网电压谐波污染小于3%;满足电力部门对用电标准。
6.系统不会由于电气系统故障而导致合成氨装置停产。
采用电压源型高压变频调速驱动系统,配套10kV供配电系统能够解决上述技术需求。从根本上,解决合成氨装置主压缩机系统的经济性与技术性的双重标准要求,实现投资小见效快,安全可靠、运营成本低的实施目的。
四、系统方案
该系统主要包括:10kV电压等级18MW合成气压缩机1台、11MW氨气压缩机1台、11.5MW二氧化碳压缩机1台。其容量均在10MW级,属超大功率旋转负载。
高压电机选用两极异步电动机驱动,采用1:3.12增速齿轮箱与与压缩机负载连接。选用电压源型单元串联多电平结构变频器,网侧功率因数大于0.95、网侧谐波污染小于3%、适用于普通异步电动机;而无需增设无功补偿或选用同步电动机。
压缩机系统采用变频驱动后,压缩机组可实现软起动、软停车功能,并且能够承受系统喘振时产生的电气瞬时过载冲击负荷,而不会保护误动。采用变频启动时的电流加速曲线如图一所示。另外,变频器可以按照合成氨装置生产所需的压缩机升速曲线实现,调节压缩机转速;其启动过程的加速特性如图二所示。
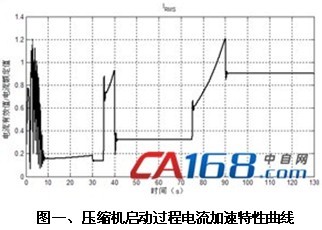
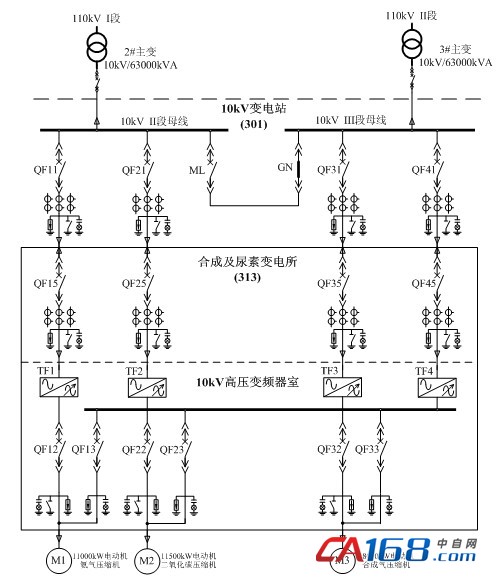
图三、高压电气配电与变频驱动一次动力系统图
厂变由两路110kV电网接入10kV高压301变电站,提供II、III两段母线变压器供电。当单段电网供电或变压器故障时,厂区可通过ML-GN依赖另外一段电源供电变压器承担生产100%用电负荷;而无需停产。
三、技术可行性分析
该40万吨合成氨装置的三台主辅机设备分别为:18MW合成气压缩机、11MW氨气压缩机、11.5MW二氧化碳压缩机。根据工艺生产对设备工况的需求,结合电气驱动的需要。电气驱动系统主要需具备以下几方面的能力:
1.采用高压电动机驱动,通过增速齿轮箱满足压缩机系统的高速运行需要。
2.能够依工艺需求,进行分阶段加减速调节控制;满足系统逐步升温、升压。
3.能够根据合成氨装置的整体生产需求进行压缩机转速、气量调节。
4.压缩机采取软启动、软停车方式,对电网和压缩机机械系统冲击负荷小于额定的2.5倍转矩;能够承受压缩机喘振产生的1.5 Tn波动负荷。
5.电气系统对电网无冲击,网侧功率因数大于0.9、对电网电压谐波污染小于3%;满足电力部门对用电标准。
6.系统不会由于电气系统故障而导致合成氨装置停产。
采用电压源型高压变频调速驱动系统,配套10kV供配电系统能够解决上述技术需求。从根本上,解决合成氨装置主压缩机系统的经济性与技术性的双重标准要求,实现投资小见效快,安全可靠、运营成本低的实施目的。
四、系统方案
该系统主要包括:10kV电压等级18MW合成气压缩机1台、11MW氨气压缩机1台、11.5MW二氧化碳压缩机1台。其容量均在10MW级,属超大功率旋转负载。
高压电机选用两极异步电动机驱动,采用1:3.12增速齿轮箱与与压缩机负载连接。选用电压源型单元串联多电平结构变频器,网侧功率因数大于0.95、网侧谐波污染小于3%、适用于普通异步电动机;而无需增设无功补偿或选用同步电动机。
压缩机系统采用变频驱动后,压缩机组可实现软起动、软停车功能,并且能够承受系统喘振时产生的电气瞬时过载冲击负荷,而不会保护误动。采用变频启动时的电流加速曲线如图一所示。另外,变频器可以按照合成氨装置生产所需的压缩机升速曲线实现,调节压缩机转速;其启动过程的加速特性如图二所示。
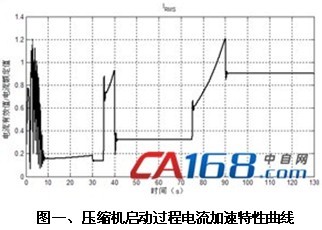
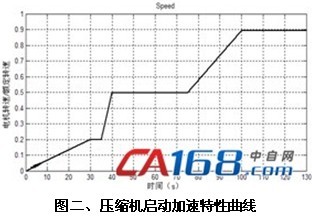
三台压缩机组的装机功率40.5MW,电网累计容量需求5.0625MVA。电气配电系统中11MW、11.5MW 采用II段母线供电,18MW及备用变频器(18MW)采用III段母线供电。每段母线网侧变压器容量均为6.3MVA可同时为两段母线负载供电;确保单段电源丢失时,单段母线保证生产连续。
方案采用全容量高压变频备用的一拖一变频切换系统方案,其原理如图三所示。其中,QF表示高压开关、TF表示变频器、ML表示母联开关、GN表示隔离开关柜、M表示电动机。QFx2和QFx3之间存在电气与逻辑双重互锁关系,防止变频器输出侧发生短路等严重事故(x,表示设备编号)。
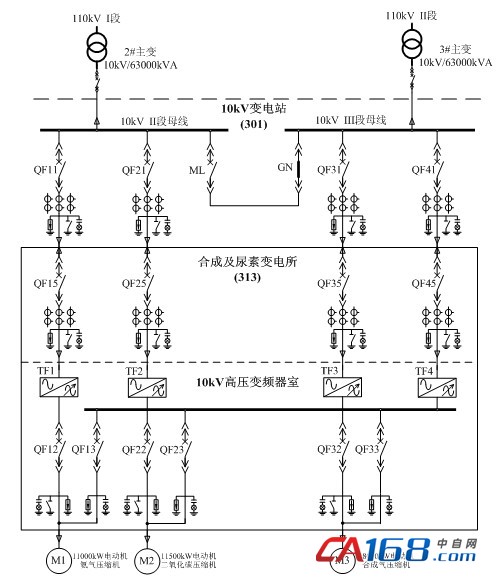
图三、高压电气配电与变频驱动一次动力系统图
厂变由两路110kV电网接入10kV高压301变电站,提供II、III两段母线变压器供电。当单段电网供电或变压器故障时,厂区可通过ML-GN依赖另外一段电源供电变压器承担生产100%用电负荷;而无需停产。
三台压缩机的电动机驱动系统,由301变电站II、III段母线分别引至313变电所。其中,备用变频器下挂于III段母线,QF41提供10kV驱动电源。备用变频器可在三台电动机任意一台工作变频电气系统故障时,驱动压缩机调速运行。
正常情况下,每台压缩机均有一台主变频器TF通过QF2连接至电动机,实现压缩机的电气驱动。系统并可根据合成氨装置的生产需求调节压缩机转速改变气量,达到满足生产的目的。
以合成气压缩机为例:压缩机主变频驱动时,首先检查备用变频器输出侧QF13与电动机处于断开状态,然后闭合工作变频器TF1输出侧开关QF12与电动机M1连接。送电启动步序:①QF13处于分断状态;②操作QF12合闸;③变频器允许高压合闸;④操作QF15合闸;⑤启动条件满足、变频器待机正常;⑥启动变频器TF1运行;⑦合成气压缩机电动机启动完毕。
当合成气压缩机主电气系统故障或需要检修时,压缩机可利用备用变频TF4提供不间断变频驱动运行。备用变频启动步序:①操作QF12分闸状态;②操作QF13的合闸,备用变频器TF4自动选择适配电动机启动保护参数组;③操作确认电动机对应的工位有效,TF4具备高压合闸允许条件,允许QF45合闸;④操作QF45合闸;⑤压缩机具备变频器启动运行条件、变频器待机正常;⑥启动备用变频器驱动压缩机组运行;⑦电动机M1变频运行恢复完毕。
备用变频器TF4自动确认电动机匹配,选择与之对应的控制功能和对应的压缩机控制工艺参数;满足备用变频器可替代合成气、氨气、二氧化碳压缩机用变频器的需求。
五、配套应用技术
在采用电气驱动系统替代“锅炉+汽轮机”的驱动方案后,系统采用变频协调控制技术解决电气系统中变频器与高压开关、压缩机组、生产工艺之间的协调控制关系,以及主变频器与备用变频器之间的切换替代等协调问题。
另外,高压变频器在运行中将产生3%的效率损失,并以热量形式散失在环境中。需要配套高压变频空-水冷却系统解决变频器的环境散热问题。通过系统化集成解决方案的应用,实现压缩机电气驱动的工艺控制、变频驱动控制、环境控制等。
六、结束语
通过对40万吨合成氨装置压缩机驱动系统的分析和实践证明,以高压变频为核心的电气驱动系统完全能够满足化工生产中对压缩机转速、气量调节的需求;并且在项目投资运营方面获得可观的经济收益。该项目的实施,为化工行业超大功率压缩机组解决能源与经济、环保、高效生产等综合问题,提供了新思路、新方法;值得在化工生产领域的能源利用、节能降耗和环保生产建设和改造项目中积极推广。
五、配套应用技术
在采用电气驱动系统替代“锅炉+汽轮机”的驱动方案后,系统采用变频协调控制技术解决电气系统中变频器与高压开关、压缩机组、生产工艺之间的协调控制关系,以及主变频器与备用变频器之间的切换替代等协调问题。
另外,高压变频器在运行中将产生3%的效率损失,并以热量形式散失在环境中。需要配套高压变频空-水冷却系统解决变频器的环境散热问题。通过系统化集成解决方案的应用,实现压缩机电气驱动的工艺控制、变频驱动控制、环境控制等。
六、结束语
通过对40万吨合成氨装置压缩机驱动系统的分析和实践证明,以高压变频为核心的电气驱动系统完全能够满足化工生产中对压缩机转速、气量调节的需求;并且在项目投资运营方面获得可观的经济收益。该项目的实施,为化工行业超大功率压缩机组解决能源与经济、环保、高效生产等综合问题,提供了新思路、新方法;值得在化工生产领域的能源利用、节能降耗和环保生产建设和改造项目中积极推广。
共0条 [查看全部] 网友评论