关键词:PLC 乳化液泵站 触摸屏 智能控制
Abstract: A design of intelligent emulsion pump control system using PLC as the control core, adopts the distributed loop control mode, through the Ethernet and touch screen to achieve the real-time control including monitoring system, information exchange, operation status display, fault diagnosis, parameter at the same time with the save function, can greatly improve the degree of automation of intelligent pumping system management.
Key words: PLC Emulsion pump station Touch screen Intelligent control
【中图分类号】TV675 【文献标识码】B 文章编号1606-5123(2017)07-0000-00
1 引言
随着煤矿综采技术的不断发展,对智能采煤技术和采煤设备的要求越来越高。乳化液泵站作为向综采液压支架输送液体的动力设备受到了越来越多的重视。传统的液泵站多采用一主一备用泵的形式,其存在自动化程度低,操作繁琐,可靠性差,需要经过专业训练的操作人员进行手工辅助和维护等诸多缺陷,逐渐被淘汰。因此,本文设计了一种基于PLC的智能乳化液泵站控制系统[4]。该系统以S7-200 SMART为控制核心,采用主泵和备用泵集散控制的方式,各泵通过传感器变送装置实时将运行状态参数发送至CPU进行处理,泵与泵之间通过以太网实现相互间的通信。为了避免各乳化液泵的运行时间不同,导致系统运行的提前和滞后,对各个乳化液泵设定优先级顺序,达到优化运行系统使用寿命的目的。通过上位机触摸屏及操作键盘装置可以实现对系统的实时监控、参数修订、信息查询等功能。
2 总体设计
系统的总体设计结构如图1所示。
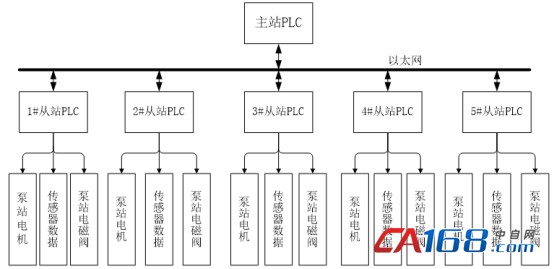
图1 总控制系统结构图
2.1 主站控制系统设计
主站控制系统结构图如图2所示。
主站控制系统作为整个智能乳化液泵站的控制核心,实时接收来自各从站传感器装置传送的油位、液位、温度等参数,完成报警、配液、补油等功能,并传送数据给HMI。除此之外主站控制器根据采集到的主管路压力值的大小来模拟工作面所需的乳化液流量,主管路压力值的变化会完成对各泵启用或停用的自动控制。整个泵站系统采用3个主泵和2个备用泵的配置,通常情况下是3个主泵在运行,随着所需乳化液流量的变化按照自适应循环策略顺次开启水泵,可以提高系统的整体使用寿命[2]。当主泵站出现故障时调用备用泵,为了保障整个系统的稳定运行,留有2个备用泵来调用。
图2 主站控制系统结构图
2.2 从站控制系统设计
从站控制系统结构图如图3所示。
各从站控制系统会实时监测运行状态,包括油位、液位、温度、压差等,并及时通过以太网将这些数据反馈给主站控制系统,主站对此进行诊断后发送相应指令。如果泵站故障比较严重,系统可以直接停用该泵、更换备用泵并发出警报,实现自动化管理。所有的这些相关信息会显示在人机交互界面中。当然各自泵站也具有自诊断功能。
图3 从站控制系统结构图
3 软件设计
为了使整个智能乳化液泵站控制系统稳定高效运行,同时提高整体的使用寿命,对3个主泵和2个备用泵设定优先级,并根据可能出现的工作状态划分3种模式,其中排在前面表示投入使用的优先级高,后面的依次类推,当退出使用时本着先进先出的原则进行控制。具体划分如表1所示。
表1 乳化液泵站控制系统的三种工作模式表
模式1 |
模式2 |
模式3 |
1号泵 |
2号泵 |
3号泵 |
2号泵 |
3号泵 |
1号泵 |
3号泵 |
1号泵 |
2号泵 |
备用泵1 |
备用泵2 |
备用泵1 |
备用泵2 |
备用泵1 |
备用泵2 |
3.1 主站控制程序设计
在主站控制器进行工作前要对其进行初始化,初始化过程中,控制器需要整体扫描,读取设定的数据,并清除寄存器中的数据进行初始化。正常运行后,各个泵按照程序设定的优先级顺序自动运行。
主站PLC从寄存器中读取从站PLC输入的监控参数数据,经过收集、处理后决定系统是否启动。如果收集到的数据参数符合启用要求,那么工作人员按下启动按钮,就能实现乳化液泵站系统的自动控制。在系统运行时,共有3台主泵和2台备用泵,3台停止运行的主泵需要完成停用后再启用的命令,系统完成启动后,各个泵站自动完成延时启用。主站运行过程控制流程图如图4所示。
图4 主站控制器控制流程图
3.2 从站控制程序设计
从站在泵站正常工作过程中的作用是,将各个泵的实时状态参数传输给主站控制器,协助主站监测整个控制系统的运行状态。主站也可以将信息发送给从站,帮助从站执行相应动作,实现信息的交互。从站运行过程如图5所示。
图5 从站控制器控制流程图
4 以太网通信及HMI
4.1 通信协议研讨
S7-200系列PLC之间通信,可以使用PPI进行数据的交换,但是对于S7-200 SMART的PLC来说其自带的485通信口不支持PPI通信,如果需要通过这个485口实现S7-200 SMART PLC之间的数据交换,以往的做法是通过这个口来做MODBUS通信,一个作为MODBUS主站,一个作为MODBUS从站,来进行数据交换。
如果两个PLC作为MODBUS通信来实现PLC之间的数据交换的工作量会比较大,会增加系统的复杂性与成本。那么S7-200 SMART PLC相对于一般的S7-200 PLC来说有一个优势,就是在PLC的基本单元上带有一个以太网口,可以使用这个以太网口来实现S7-200 SMART PLC之间的数据交换,并且使用以太网通信可以实现8台PLC之间的数据交换,非常高效简便。
4.2 人机界面设计
控制系统人机界面主界面主要显示以下信息:①通信,显示主从站控制器之间的通信状态,正常通信时显示绿灯,故障时显示红灯;②电磁阀,绿灯表示电磁阀开启,红灯电磁阀关闭;③过载、漏电:当出现这些故障时警示灯显示红色,正常情况下为绿色;④运行状态,实时显示主从站的运行状态,包括主从站的参数检测,显示在主界面中[3]。主界面设计图如图6所示。在登录人机界面系统进行修改相关参数时,需要以管理员的身份登录,输入及设置的参数必须在传感器可测范围内,否则将无法进行保存设置。当某一实时数据超过设定值或某一设备出现故障时,进行报警并作相应处理,报警后将所需参数存入数据库中,供日后查询。
图6 人机主界面设计图
5 结束语
针对目前矿井乳化液泵站的发展状况,设计了一种基于PLC的智能乳化液泵站控制系统,系统采用集散式循环控制方式,实时监控泵站系统设备运行状态,并显示在人机界面中。当出现故障时,系统直接停用、更换相关泵并发出警报。具有实时监控、自动控制、故障诊断、参数保存等功能,可以大大地提高采煤效率,实现泵站自动监控及采煤自动化。
参考文献
[1] 吴志刚,罗剑,肖世德.基于PLC实现的乳化液泵站控制系统的技术改造[J]. 矿山机械. 2007(05).
[2] 范静.基于ST-200PLC智能控制乳化液泵站的设计开发[D]. 电子科技大学. 2010.
[3] 张盼盼.乳化液泵站自动监控系统的研究与开发[D]. 太原理工大学. 2009.
[4] 谢云昌.基于PLC的乳化液泵站状态监控系统[J]. 煤矿机械. 2013(03).
[5] 袁任光.集散控制系统应用技术与实例[M].机械工业出版社,2003.
作者简介
任辉 男 硕士在读 研究方向:电力电子与工业自动化工程
共0条 [查看全部] 网友评论