Abstract: Composite brake drum, robot loading and unloading, unmanned production, cutting fluid cleaning.The composite brake drum is a special product for heavy trucks. The processing of this product requires high processing accuracy and heavy weight. There are several problems in mechanical processing: 1. The weight of the product is heavy, each brake drum is about
Key Words: Brake drum Robot Loading and unloading Cleaning
【中图分类号】TP242 【文献标识码】B 文章编号1606-5123(2018)04-0000-00
1 引言
目前,国内生产使用的制动鼓大部分采用灰铸铁材料,不足之处在于载重汽车刹车常用的交替制动发生冷热交替现象而发生开裂、龟裂、掉底、磨损过大引发安全事故。复合制动鼓是把原来传统的全铸铁的制动鼓,变为外层整体钢壳、内层耐磨铸铁的双金属复合一体式制动鼓,克服了传统制动鼓无韧性、易开裂的缺陷。是为避免载重汽车制动鼓在高速行驶、下长坡等坡情况下易破裂而研发的新产品。但是该产品的加工对操作者的搬运、安装、产品一致性有很高要求,废品率难以控制。对比成本会高于普通制动鼓60%。通过加工过程的自动化提高合格率、降低人工参与风险是急需解决的问题。
2 工艺系统分析
2.1 加工工及方法
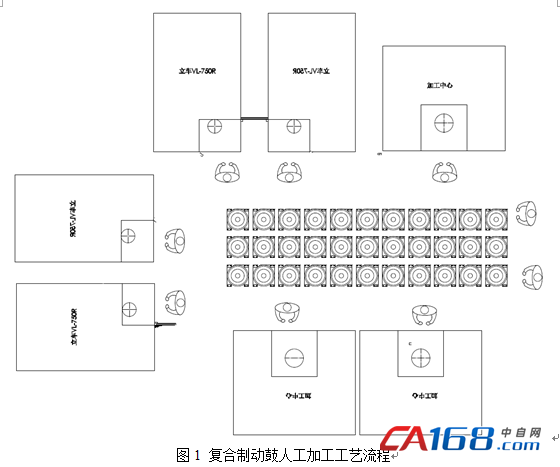
2.2 DZ91106型制动鼓抓取工艺
立式加工中心VL-750R负责加工产品内表面,机器人抓取面为产品内孔,工艺过程参见如图2所示。
2.4 0144型制动鼓抓取工艺
立式加工中心VL-850A负责加工孔,机器人抓取面为产品外表波浪面如图3所示。
图2、图3所示的工件移位过程,如果是由人工组装操作,,则现场每台加工机床需要配置一名操作工,总计6台设备可以出一件成品。这样需要6名操作人员,还有2名毛坯和成品的物流配合人员。由于产品比较重,整体产品的合格率只有50%。
3 机器人移位实现
3.1机器人抓手选型计算
机器人抓手选择一台机器人安装2套抓手,一个抓手下料,另一个抓手上料,可以节约时间。这样就需要仔细计算机器人的负载问题。
负载计算:产品最重50㎏,两件产品则为100㎏;根据产品图纸,机器人的抓手需要一套抓取内孔(如图3),一套抓取外圆(如图4)。选择采购ZIMMER公司的三爪抓手。初步选型为GPD5025SC和GPD5025SO:
相关抓手参数如表1所示。
表1 ZIMMER三爪抓手参数表
序号 |
内容 |
GPD5025SC |
GPD5025SO |
1 |
单指行程(mm) |
14 |
14 |
2 |
关闭力(N) |
22270 |
|
3 |
打开力(N) |
|
22850 |
4 |
关闭时间(s) |
0.6 |
1 |
5 |
打开时间(s) |
1 |
0.6 |
6 |
推荐单个手指重量(㎏) |
7 |
7 |
7 |
产品重量(㎏) |
17.6 |
17.6 |
计算如下:
钢与钢的静摩擦系数:0.05;
外圆抓手选择:
GPD5025SC的外圆夹紧力:0.05×22270=1113.5(N)=111.35(㎏)
使用该抓手气缸的安全系数:111.35÷50≈2.2
根据机械设计手册,在中载行业,该安全系数合适。
内孔抓手选择:
GPD5025SO的内孔撑紧力=0.05×22850=1142.5(N)=114.25(㎏)
使用该抓手气缸的安全系数=114.25÷50≈2.3
根据机械设计手册:在中载行业,该安全系数合适。
同时单个手指行程为14mm,在抓取产品时给与产品比价合理的外形误差范围。建议客户的零件外形误差一致性不大于4mm。
按照以上计算,机器人总计要承担的负载为:
G=2套产品重量+2套抓手重量+6根手指重量+线缆等
初步机器人至少需满足的负载能力为:
G=50+50+17.6+17.6+6*7(抓手手册推荐数据)+1(经验数据)=178.2(㎏)
3.2抓手机械设计
抓手的设计分别抓取外圆和内孔。同时外圆抓取曲面,所以加工时要标注为仿形加工。由于抓取过程中要注意产品是否在机械手上,所以要安装接近开关,当产品抓取到,会有信号给机器人,表示可以进行下一步动作。如果没有信号,表示没有抓取到位,等待人工检查。同时三爪抓手的最大优势,是可以自动找到圆形产品的中心线,实现“自动定心”的目标功能。
外圆抓手设计图参见图4所示。内孔抓手设计图如图5所示。
3.3机器人初步选型
参见3.1机器人抓手选型计算,机器人的负载能力要大于178.2㎏。选择安川机器人,初步选型MS210机器人,可以承载210㎏的负载。机器人的负载安全系数为210114.25÷178.2≈1.2。满足轻载项目需求。仔细考虑机器人的动作过程,首先机器人同时抓取两个产品的时间只有抓取加工完成的产品,另一个手抓取要放下的产品交替过程阶段,其余都是只抓取一个产品。另外,机器人的运动动作在该项目中不能太快,否则一旦发生产品抓取不牢,产品飞出去会造成极大的安全事故。所以选择初步选择MS210机器人。该机器人的外形图及相
关参数如图6所示。机器人控制柜外观如图7所示。
3.4切削液清理
加工完成后,内孔表面的切削液和刀屑之前需要人工拿压缩空气吹干净,但是产品重量重,人工操作比较难,需要自动化。设计思路:设计支架,上面安装多个吹气嘴,机器人抓取产品上下运动,使内表面可以都被压缩空气吹到。机器人动作次数可以在系统中修改。下方的
抽屉可以接取废料,到一定时间人工清理。切削液自动吹气机构如图8所示。
3.5方案布置图设计
方案布置图的设计,首先优化现场布局图,同时工艺满足。
(1)来料状态:产品基本成型(离心铸造),298mm内孔朝下放置。机器人需要首先抓取410mm内孔上下料:第一序:机器人抓取410mm内孔工件,放置到4台立车,精加工410mm内孔。第二序:将产品翻面,精加工298mm内孔及10个23mm圆孔。需要2台加工中心就可以匹配整体的加工节拍。
(2)加工完成,清洗内:输出,同时表面激光雕刻二维码。整体节拍10分钟/件。
根据该加工工艺,制作方案布置图初稿如图9所示。
整个方案需要2名操作者,一名操作复杂在上料台车附件给托盘上料,一名操作者偶尔进行抽检。而产品的输出总结通过输送线输送至下一个车间。
3.6节拍计算
整个项目的节拍,10分钟完成一件产品,而机器人的动作速度为:S轴水平运动120°/s。我们按照机器人的动作范围约360°(四台立车到过渡台)。运转速度不能太快,按照20%的速度运行,则S轴运行360°,需要15秒。一个流程机器人需要实现:
(1)抓取(4s)+提升(4s)+平移(15s)+下降(4s)+抓取(4s)+旋转抓手(4s)+放置过渡台(15s)+返回原点(15s)=65(s)。一台机器人足够应对4台立车。
(2)同理,计算另一台机器人应对2套加工中心:
过渡台抓取(4s)+提升(4s)+平移(15s)+下降(4s)+抓取(4s)+旋转抓手(4s)+ 返回原点(15s)=50(s)。一台机器人足够应对2台加工中心。
4 新增设备配置
4.1上料台车
台车属于气缸推动料盘结构,制作2套。每个料盘放置4个产品,加工完成后循环使用。空图盘运行至安全栏外,人工装料。装料完成的自动进入安全栏内,机器人抓取,每个零件是否放置到位都有开关检测。实现不停机生产。而每次人工装料的时间约4个零件=8分钟,加工完成4个零件的时间为40分钟,操作者至少可以休息20分钟,大大降低了劳动强度。
入料台车如图10所示。
4.2过渡台
用于将R1加工完的零件放置到位,方便R2机器人抓取内控表面。同时根据空间最大可以放置4个零件,也就是意味着当R1发生问题时,R2机器人还可以抓取4个零件,有40分钟的维修时间。给维修者提供了更加充足的时间余量。每个支架上安装开关,检测是否放置零件,机器人会根据空位信息自动补齐零件。过渡台如图11所示。
4.2 安全围栏
整个系统设计安全围栏,避免人工进入区域发生事故。围栏选择丝网状,既可以参观到内部生产情况,又可以避免人员进入。只有操作者打开安全门,系统所有设备立即停止动作,等待人工复位方可工作。安全围栏如图12所示。
5 PLC系统控制
项目控制系统部分采用PLC控制,PLC程序具有自动、检测、保护、报警等功能,并能显示各单元的运行状态,包括:急停监控界面、站状态监控界面、错误监控界面、自动/手动及强制操作与监控界面、维修界面、所有动作位置、输入、输出信号当前状态界面等。
控制系统有自动、手动、强制、空循环运行方式选择和当前运行方式指示。
自动运行(单循环)方式:在原位状态,外部放置工件后,通过按钮启动,设备自动完成所有动作循环,返回到原位状态,并给出循环完成指示信号(柱状指示灯),该循环停止。启动设备在自动运行循环过程中出现故障,手动方式或其它手段把故障排除后,设备仍可以在停止位置再启动,并完成该自动循环的工作。
手动方式:设备的各种互锁有效,在保证无设备及人员伤害的情况下,设备的所有可运动装置都可单独手动控制运动,选择运动装置及运动方向后,在执行按钮按下时,开始执行该动作,直至该动作完成。对于可中途停止的设备装置,如果动作未完成前执行按钮松开,则动作停止,再次按执行按钮可继续执行。
强制方式(钥匙开关):与手动方式的区别在于,除安全互锁信号有效外,其它互锁信号无效,其它部分与手动相同。
空循环方式:设备可以在没有工件的情况下,能够完成整个控制系统连续多循环自动运行。
当出现故障时,能显示故障详细信息。控制柜设控制电源开关,使用取插钥匙式,左转为切断,仅左转能拔出。
6 结束语
根据以上过程的研发设计,研发改造通过2台MS210机器人,结合4套三爪抓手、中转台、上料机构、测试线、PLC系统实现了自动化设备之间上料、下料、定位均无人参与全自动化运行。整个生产至少每个零件至少节约了15分钟,省去操作人员6人。同时所有的运行数据、生产数据、二维码信息等全部可以接入MES系统,为车间下一步的智能生产做准备。该项目作为全国第一套复合制动鼓加工机器人自动化项目,不仅降低了成本,还从50%的合格率上升到92%的合格率,推进工业4.0的发展。
参考文献
[1]成大先.机械设计手册(第五版).北京:化学工业出版社,2008.
[2]德国ZIMMER公司.气动MKS系列产品说明书,2018.
[3]亚德客国际集团.亚德客综合型录2017.
[4]喜开理(中国)有限公司.CKD综合型录2017.
[5]陈国华.机械结构及应用.北京:机械工业出版社,2008.
[6]安川电机(中国)有限公司.产业用机器人MOTOMAN系列综合样本,2016.
共0条 [查看全部] 网友评论