第四章 石油化工行业
第八节 制药厂压缩机组变频调速节能改造
一、工程概况
河南天方药业有限公司的前身是成立于1969年的驻马店地区制药厂,经过几代天方人的不懈努力和奋力拼搏, 并于2000年12月在上海证券交易所挂牌上市。天方药业股份有限公司是以新药开发、化学原料药、生物原料药、中药及成品制剂生产、销售为主的大型医药工业企业,是全国512家重点企业之一,也是国家科技部和中科院共同认定的高新技术企业.下属有5个子公司、1个技术开发中心、80个驻外 办事处。现有员工3000余人。资产总额15亿多元。年产片剂68亿片,居亚洲第一位,拥有抗生素发酵吨位5000立方米,居全国同行业第二位,年产乙酰螺旋霉素500吨,居全国第一位。
压缩机设备参数:
河南天方药业集团二分厂共有各种类型压缩机31台:650m3/min进口离心式压缩机4台,400 m3/min国产离心式压缩机11台,国产活塞式压缩机(80m3/min)16台,它们的设备参数和工作数据如下:
(1) 进口离心式压缩机4台:
压缩机参数:
型 号:TA95M2D (双路并联压缩)
额定流量:650m3/min
吸气压力:0.0993MPa (大气压力0.1013MPa)
吸气温度: 35 oC 相对湿度: 80%
排气压力:0.33MPa (绝对压力)
轴 功 率: 2058 kW (±4%)
电动机参数:
型 号:TECO 三相感应电动机
额定功率:2200kW
额定电压:10000 V
额定电流:139 A (运行电流 118-122A)
额定转速:2980 rpm
功率因数:0.88
(2) 国产离心式压缩机11台:
压缩机参数:
型 号:
额定流量:400m3/min
吸气压力:98.68 kPa (大气压力100.68 kPa)
吸气温度: 20--155 oC 相对湿度: 80%
排气压力:280.68 kPa (绝对压力)
轴 功 率:1098 kW (±4%)
电动机参数:
型 号:YKOS 1250 --2 三相感应电动机
额定功率:1250kW
额定电压:10000 V
额定电流:84 A (运行电流 78-82A)
额定转速:2985/17601 rpm (速比:5.89 ?)
功率因数:0.85
(3) 国产活塞式压缩机16台: (用作末端压力微调。)
压缩机参数:
型 号:
额定流量:80m3/min
吸气压力:98.68 kPa (大气压力100.68 kPa)
吸气温度: 20--155 oC 相对湿度: 80%
排气压力: 320 kPa (绝对压力)
轴 功 率: 208 kW (±4%)
电动机参数:
型 号: 三相感应电动机
额定功率:240kW
额定电压:380 V
额定电流: 54 A
额定转速:1485 rpm
功率因数:0.85
图1所示为201车间压缩机组的示意图:
(4)设备运行状况介绍
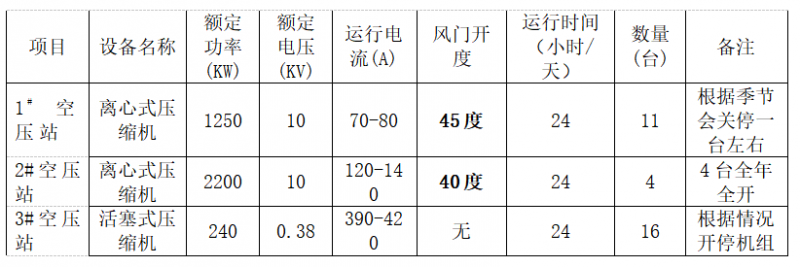
图1 河南天方药业集团二分厂压缩机组分布示意图
二、压缩机组运行工艺分析:
二分厂的中央供气系统是由3个空压站共同组成的中央网管集中供气系统,主要为各个车间提供温度与压力适宜的压缩空气,压缩空气主要用于各车间发酵罐补充氧气之用,其用气量与各车间发酵罐的开机程度,及发酵周期时间段成周期性变化,且跟季节气温的变化也有关系。
中央供气系统由于负载变化性较大,且压缩机都属于大型动力设备,并多为直接启动或降压启动方式,不适合采用频繁停启压缩机作为调节压缩机应对负载突变引起的气压变化的手段,目前采用的是调节进气阀门开度大小来控制供气压力变化,且阀门控制采用的是手动控制,只能粗糙的对气压变化实施调节,使多数压缩机处于轻载并处于高耗能工作状态,尽管操作人员为此付出了不懈努力,但由于硬件设备条件的限制,目前的运行现状就是如此。所以对压缩机实施变频节能改造已迫在眉睫,尽管高压变频设备高昂的价格往往让用户望而怯步,但在高新技术高速发展的今天,高压变频器的价格已大幅度下降,已能为广大企业所接受;同时国家也对节能减排高度支持,出台了一系列优惠政策,为企业节能改造工作提供了良好的条件。
(1)根据目前生产用气量只有运行压缩机出力的50%,而管网压力(0.16MPa)也未达到其额定压力的情况下,电动机的运行电流已达到90~95%,说明压缩机的运行效率较差,原因是其控制方式(进口风门)造成的。
(2)夏天时由于温度高,需氧量大,要求进气量大;同时由于温度高,空气密度低,也要求进气量大,所以要求开大风门(但受电机电流限制)只有通过增加运行台数来满足用气需求;而冬天则相反。
(3)要求目标是进气量(供氧量),以满足发酵罐的工艺要求,压力可以适当降低,从而最大限度地挖掘节能的潜力。如将供气压力降低到1.4kPa,则2200kW压缩机和1250kW压缩机都有较大的节能效果,至于240kW活塞式压缩机则与供气压力无关(出口压力0.22MPa)。(4)压缩机装机设备总流量:8280m³/min, 冬季实际用气量50%左右,夏季实际用气量约为65%左右,都有很大的富裕量。目前650 m³/min压缩机开4台、400 m³/min压缩机开10台、80 m³/min压缩机开5台,总流量为7000m³/min,而生产用气量仅为3958 m³/min,占供气总量的56.5%;而2200kW进口压缩机的运行电流已达118~120A,1250kW国产压缩机的运行电流已达78~82A,均已接近额定电流。
由于管网阻力很大,因此不允许将进气门开大(否则电动机将过载),夏天由于空气密度变小,所以当进气门开大时,其电功率增加并不多。由目前的用气量和电动机的运行电流来看,压缩机组运行很不经济,其原因是压缩机在小流量工作时的效率大幅度降低。
三、 变频调速节能分析
由于所有的压缩机都并入同一管网系统工作,管线很长,所以管网阻力很大。离心式压缩机采用进气门控制,活塞式压缩机则采用运行台数控制。在目前(冬季)用气量约为60%左右,管网压力为0.16MPa(表压,即相对压力)的工况下,压缩机运行电流已达90%—98%,若再开大进气门电动机就会过载;夏天由于空气密度变小,所以进气门要开大,而电功率增加并不多。由于压缩机在小流量工作时效率降低,所以电流太小工作不经济;由于压缩机台数很多,所以可以采用工作台数来调节用气量,让所有运行压缩机都工作在高效状态。由于管网阻力很大,还要保证进入发酵罐的压力,所以管网压力应满足不小于0.15MPa。
各压缩机站工频耗电情况:
1#空压站
1#~11#离心式压缩机每台工频运行功率
=10×78×1.732×0.8
=1080KW
其中,每台电机额定功率为1250KW,额定电压为10KV,平均运行电流为78A,其中实际运行功率因数取0.8 。
总耗电功率约为:1080*11=11888KW即每小时耗电11888度。
2#空压站
1#~4#压缩机每台改造前工频运行功率
=10×118×1.732×0.8
=1635KW
其中,每台电机额定功率为2200KW,额定电压为10KV,平均运行电流为118A,其中实际运行功率因数取0.8 。
总耗电功率约为:1635*4=6540KW即每小时耗电6540度。
3#空压站
1#~16#压缩机每台改造前工频运行功率
=0.38×390×1.732×0.9
=231KW
其中,每台电机额定功率为240KW,额定电压为380V,平均运行电流为390A,其中实际运行功率因数取0.9 。
总耗电功率约为:231*10=2310KW即每小时耗电2310度。
图2 压缩机组的综合性能曲线和调速分析
图2为两组共15台压缩机组的综合性能曲线,第一组为11台额定流量为400m3/min,出口全压为0.18Mpa的国产压缩机,第二组为4台额定流量为650m3/min,出口全压为0.23Mpa的国产压缩机;选择出口压力较大的四台进口压缩机变频调速改造,可以取得较好的节能效果。
由图2可以看出:压缩机组目前的工作点在M,总流量约为6800 m3/min,压力为0.16Mpa;若将四台进口压缩机关掉(或者将转速降低到足够低,以至于不能并气),压缩机组的工作点将移到B点,流量为5400 m3/min,压力为0.11Mpa,总的轴功率约为:Pz = P×Q/f = 90×110/0.85 = 11647 kW,11647kW/11 = 1059 kW,尚未超过额定轴功率(1098kW),所以电动机也不会过载。
对于变频压缩机组来说,其静压约占全压的50%,取平均调节流量为额定流量的50%计算:其转速为83.4%额定转速,管道压力约为0.14Mpa,轴功率为58%,节电率为14.5%;若流量为60%,节电率为25.8%;若流量为70%,节电率为21.3%;若流量为80%,其转速为91.8%额定转速,管道压力约为0.15Mpa,节电率为16.1%;若流量为90%,节电率为9.4%;如下表所示:
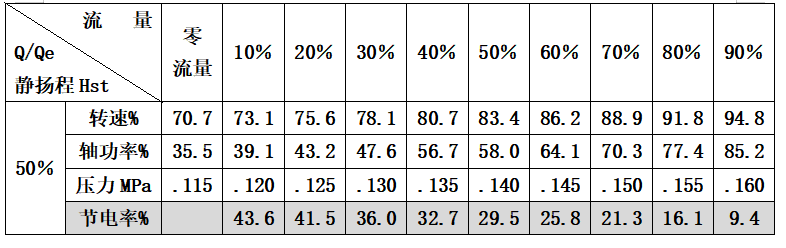
若只有一台压缩机采用变频调速的话,其静压为0.15Mpa,约占全压的65%,如图3所示。
图3 进口压缩机组的调速性能曲线
取平均调节流量为额定流量的50%计算:其转速为88.4%额定转速,管道压力约为0.14Mpa,轴功率为69.1%,节电率为14.5%;若流量为60%,节电率为13.2%;若流量为70%,节电率为11.3%;若流量为80%,其转速为94.1%额定转速,节电率为8.1%;若流量为90%,节电率为5.4%;如下表所示:
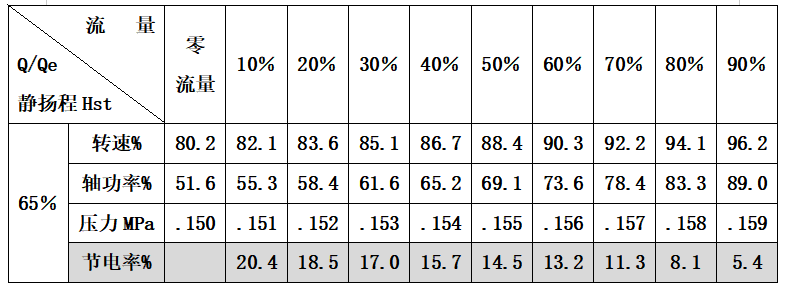
如果反过来:进口压缩机组工频定速运行,国产压缩机组变频调速运行,则其静压为0.144Mpa,约占全压的80%,见图4所示:
图4 国产压缩机组的调速性能曲线
节能计算结果如下表:
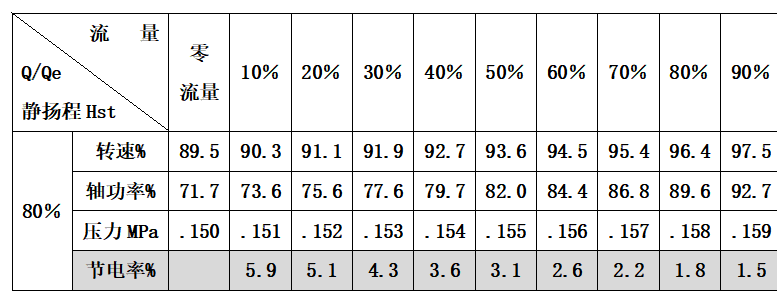
在这种情况下,如果只有一台压缩机采用变频调速运行的话,就更不能取得什么节能效果了!
相反,若是所有的离心式压缩机(包括进口和国产共15台),都采用变频调速控制的话,则其节能效果都将大大增加,估计进口压缩机组的节电率将超过20%(20%~30%左右),国产压缩机的节电率也将超过10%(10%~15%左右)。
四、变频改造实施方案
根据现场数据及设备配置情况分析,系统共分三部分组成,国产11台1250kW离心式压缩机为主力压缩机组,进口的4台2200kW机组为全自动稳压机组,16台240kW活塞式机组为系统末端压力维持机组,整体为网管并联运行,现有系统压力要求为158kPa-160kPa。各类压缩机组的额定参数和出力情况如下:
1)进口的4台压缩机组为全自动稳压机组,其流量为650 m³/min,全压为230kPa,额定轴功率为3150kW,而配套电动机的功率为 2200kW;
2)国产的11台压缩机组为主力机组,其流量为400 m³/min,全压为180kPa,额定轴功率为1500kW;而配套电动机的功率为 1250kW;
3)国产的16台低压活塞式机组,其流量为80 m³/min,全压为220kPa,其额定轴功率为365kW,而配套电动机的功率为 240kW;
4)目前650 m³/min开4台、400 m³/min开10台、80 m³/min开5台;总供气能力为:7000 m³/min.。现有生产用气量:3958 m³/min;占供气总量的56.54% ;冬季实际用气量约50%左右,夏季用气量约为65%左右,可见压缩机相当大一部分流量未发挥出来。
从现有开机数量与生产需求用气量量分析,压缩机效率较低,仅为60%左右,造成压缩机效率低下的原因固然与压缩机本身的调节方式有关,但也与压缩机与电动机的功率匹配有很大的关系:因为由压缩机的额定流量和额定全压计算得出的压缩机的额定轴功率来看,进口压缩机至少应配3150kW的电动机,国产离心式压缩机应配1600kW的电动机,而活塞式压缩机至少应配355kW的电动机。由于电动机的配置功率均小了30%左右,造成目前压缩机的进口风门不能开大,当风门开度接近50%时(此时流量约为80%左右)电动机就会过载的情况。如需加大流量,又不能使电动机过载,就只能增开压缩机的台数,而压缩机在此时的流量下并未达到额定效率,因此目前的控制方式是在牺牲压缩机的工作效率下满足流量和压力要求的,致使能耗居高不下!
要解决这个问题的最好方法是采用变频调速,将压缩机的入口风门开到最大,使压缩机在额定效率下运行,因为离心式压缩机在调速运行时的效率可在很大的范围内基本保持不变,只有当转速低于40%额定转速时才有明显下降,压缩机的运行效率可平均提高20%!
当采用变频器对电机进行调速来满足流量和管网压力要求时,由于离心式压缩机的特性为:流量与电机转速成正比,出口压力与转速的平方成正比,而轴功率则与转速的三次方成正比(但以上特性是需在无系统反压的状态下才成立)。就出口压力而言,在满足流量要求的时候,会比入口门控制时稍有下降,由此可以看出,我们在满足管网压力的同时,流量比用风门调节时还稍有富余,完全可以满足生产对流量的要求。而压缩机的轴功率却比采用风门调节时有明显的下降,这就是离心式压缩机变频调速的节能原理。但为满足其中无管网系统反压的条件,最好是每台工作压缩机都采用调速控制方式,共同满足系统压力要求,(因为工频运行压缩机的出口压力会成为变频运行压缩机的管网系统反压,)至少也应使出口压力较高的机组采用调速控制方可实现节能目的。
通过以上的分析,决定首先对四台进口压缩机组进行变频调速改造,在取得预期的节能效果以后,再对国产的11台压缩机组进行改造。致于16台活塞式压缩机组,是作为末端压力调整用的,平时开机台数较少,一般只开5台左右,并且活塞式压缩机组在进行变频运行时节能效果也较差,所以暂不进行改造。
1. 由于供气系统中有很多压缩机同时并列工作,所以当其中的某一台压缩机的变频器因故障而退出运行时,可以通过手动控制方式将该压缩机切换至工频运行,故每台变频器均配置 “一拖一”手动旁路柜,变频控制系统电气主回路如图5所示:
图65 高压变频调速系统一拖一手动工频旁路系统图
2. 根据现场安装场地的情况,设计建立6个变频器房:进口压缩机组的变频器分两个机房安装,国产压缩机组的变频器分三个机房安装。考虑到制药厂的现场环境还比较干净,且地处中原地区,夏季气温不是太高,所以变频器房的通风散热方案采用柜顶风道将热风排出室外,室外的冷空气通过进气口经滤网进入室内完成空气交换。不用安装空调,以减少投资成本和运行能耗。
3. 供气系统的控制模式采用PID恒压控制。针对原有供气控制方式存在的诸多问题,采用国产高压变频调速器对上述压缩机组进行恒压供气控制。采用这一方案时,我们可以把管网压力作为控制对象,压力变送器将管网压力P转变为电信号送给PID智能调节器,与压力设定值P0作比较,并根据差值的大小按既定的PID控制模式进行运算,产生的控制信号送变频调速器,通过变频器控制电机的工作频率与转速,从而使实际管网压力P始终接近设定压力P0。由于两种压缩机组的参数不同,所以同一设定信号时的工作频率是不一样的,需要进行折算,使两种压缩机组在不同频率下工作,但出口压力相同,不至于相互形成反压,以最大限度的挖掘节能潜力。
图6 恒压控制系统图
在以上PID恒压控制模式下,我们根据用户现场的需要,把压力设定值P0设定为0.15 MPa,当用户生产用气量加大,管网压力低于0.15 MPa时,变频器输出频率增加,电机转速加快,空气压缩量增大,压力随之上升;当生产用气量减少,管网压力高于0.15 MPa时,变频器输出频率减小,电机转速减慢,空气压缩量减小,压力随之下降,始终使管网压力保持在0.15MPa左右,大大提高了供气质量。
同时,由于该方案可具备工频与变频切换功能,并保留原有的控制和保护系统;另外,采用该方案后,压缩机电机从静止到旋转工作可由变频器来启动,实现了真正的软启动,避免了启动冲击电流和启动给压缩机带来的机械冲击。
五、经济效益评估
1.第一期改造工程:
第一期改造工程仅对四台进口压缩机组进行变频调速改造,因为四台压缩机是同一型号的,所以可以在同一频率下运行。设定出口压力为0.155MPa,运行频率为45Hz,实际测量的电功率为1373kW,节省的电功率为262kW,节电率为16%;设定出口压力为0.15MPa,运行频率为43Hz,实际测量的电功率为1292kW,节省的电功率为343kW,节电率为21%;与预估的节电率是吻合的。
若节电率按16%,每年的运行时间按7200小时,电价按0.65元/度计算,则:
每台压缩机每年可节电188.64万度,节约电费122.62万元;合标准煤650万吨,可减少二氧化碳排放1627万吨。
若节电率按21%,每年的运行时间按7200小时,电价按0.65元/度计算,则:
每台压缩机每年可节电246.96万度,节约电费160.52万元;合标准煤852万吨,可减少二氧化碳排放2130万吨。
2.第二期改造工程:
第二期改造工程对10台国产压缩机组进行变频调速改造,因为与四台进口压缩机组的参数不同,所以有一个转速匹配问题。经过反复试验,当进口压缩机组的工作频率为40Hz,国产进口压缩机组的工作频率为44Hz时,出口压力相同为0.15MPa,实际测量的节电率进口压缩机组为28%;国产压缩机组为15%;与预估节电率基本吻合。
进口压缩机节电率按28%,每年的运行时间按7200小时,电价按0.65元/度计算,则:
每台压缩机每年可节电329.62万度,节约电费214.25万元;合标准煤1137万吨,可减少二氧化碳排放2843万吨。
国产压缩机节电率按15%,每年的运行时间按7200小时,电价按0.65元/度计算,则:
每台压缩机每年可节电116.64万度,节约电费75.82万元;合标准煤402万吨,可减少二氧化碳排放1006万吨。
以上的实测结果证明,第二期的改造也是必要的:它不仅本身取得了可观的节能效果,而且也提高了第一期改造的节电率,真是收到了一举两得的效果!
共0条 [查看全部] 网友评论