摘要:在张力控制收放卷工艺中,使用张力计闭环方案可以使最终成品质量提升,提高工厂运行效率。但使用张力计闭环方案时,对于变频器的转矩输出精度有相应的要求。施耐德变频器第五代电机控制算法(AEMC)改善了转矩输出精度及动态响应性能,在全速度范围内可以将输出转矩精度控制在1%以内。在无溶剂复合机收卷工艺实际应用中,使用集成了AEMC算法的ATV930系列变频器成功的解决了加速阶段出现的松膜及断膜问题。
关键字:张力控制;转矩精度;AEMC;ATV930变频器;无溶剂复合机
1.引言 制造生产纸张、金属、光纤、塑料薄膜等过程中都需要用到收放卷工艺,其工艺要求生产时的材料张力控制在一定范围以内。收放卷过程中的张力控制精度会直接影响到产品的质量和工厂的运行效率。传统的张力控制主要通过摆杆传感器方案来调节电机速度方式来实现,但此方案下系统张力波动较大,最终成品的质量稳定性不高。另一种控制方案是直接通过控制系统张力,通过张力传感器检测系统张力,从而构成张力反馈系统来实现。实践证明,使用张力计方案的最终成品质量稳定性要高于摆杆方案。但在张力计方案中,对于变频器的扭矩控制精度要求提出了很高的要求,变频器需要具备在低频扭矩输出时满足一定的精度和稳定性要求的能力。施耐德变频器第五代电机控制算法(AEMC)采用国际上最新的矢量控制策略,在全速度范围下能够控制输出转矩控制精度至1%,完全匹配张力控制工艺对于变频器扭矩控制精度的要求。在实际应用于无溶剂复合机的收放卷工艺中,采用施耐德新一代集成了AEMC矢量控制算法的ATV930系列变频器,成功的实现了无溶剂复合机对于变频器扭矩输出的精度和稳定性需求。
2.张力控制方案介绍
2.1. 张力控制的收卷系统构成
张力控制的收卷系统构成图1所示。整套系统由收卷变频器、收卷电机、张力计、过渡辊、主速度辊构成。
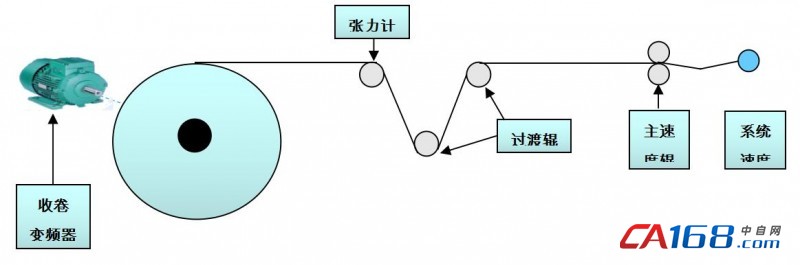
图1 张力控制的收卷系统构成示意图
系统速度由前序工艺决定,主速度辊起到隔离前道工序,即放卷张力对收卷张力的影响;张力计的安装通过过渡辊来调整及校准;系统的张力精度主要通过收卷变频器来控制电机输出扭矩实现,要求变频器工作在力矩模式,且具备输出相应的转矩精度要求。
2.2.张力控制系统理论分析
张力控制系统工作在功率恒定状态,随着负载设备的卷径由小及大,所需要的电机转速也在逐渐降低。系统所需的收卷力矩却随着电机速度的降低而增大。收放卷系统示意图如图2所示。
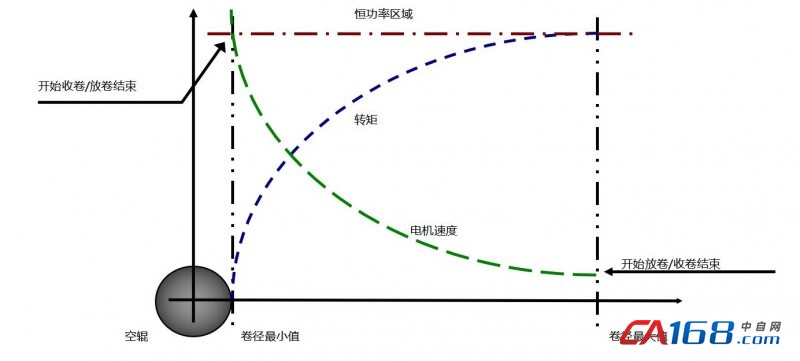
图2 收放卷系统示意图
在整套系统当中,为了便于应对各种工况,我们必须计算考虑以下参数:薄膜张力、系统线速度、加速时所需扭矩等。
薄膜所需张力:在静止状态下,忽略静态摩擦力,在轴方向上所需的张力大小直接和薄膜辊筒的半径有关,即:
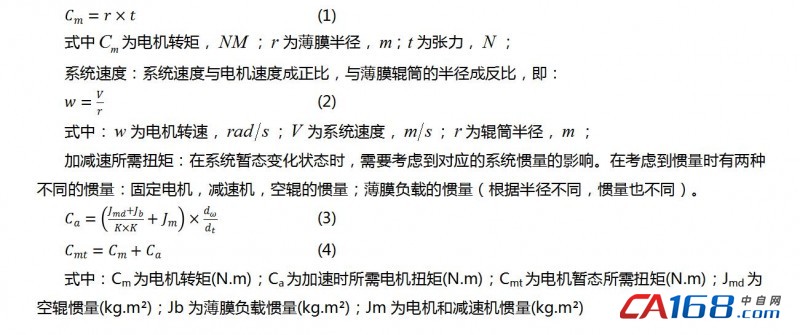
3.施耐德变频器第五代电机控制算法(AEMC)简介
AEMC算法是施耐德电气最新推出的Altivar系列变频器所采用的第五代电机矢量控制算法。 第五代电机算法(AEMC)改善了转矩精度和速度响应,增加了新的动态自整定功能,可以应用于开环及闭环控制。
3.1.转矩精度提升
得益于施耐德最新一代矢量控制算法(AEMC),变频器可以在闭环控制时实现小于1%的标称扭矩误差。与传统的电机控制方法相比(例如,市面上常用的矢量控制、DTC等),性能有显著优势。跟施耐德前一代控制算法相比,AEMC矢量控制将转矩精度提高25个百分点。控制转矩误差对比图如图3所示。
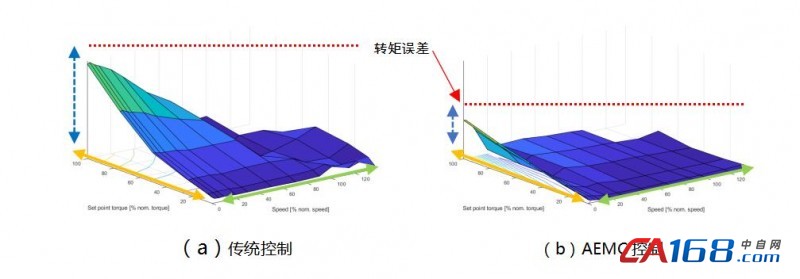
图3 传统矢量控制与AEMC控制转矩误差对比图
3.2.动态响应能力提升
第五代电机算法改善了动态速度响应。无论负载和控制类型(速度控制、转矩控制),AEMC都能在较短的响应时间内达到稳态。它可以将绝大多数负载应用的速度响应时间减少约40%。控制响应时间对比图如图4所示。
3.3.动态自整定功能
4 无溶剂复合机收放卷
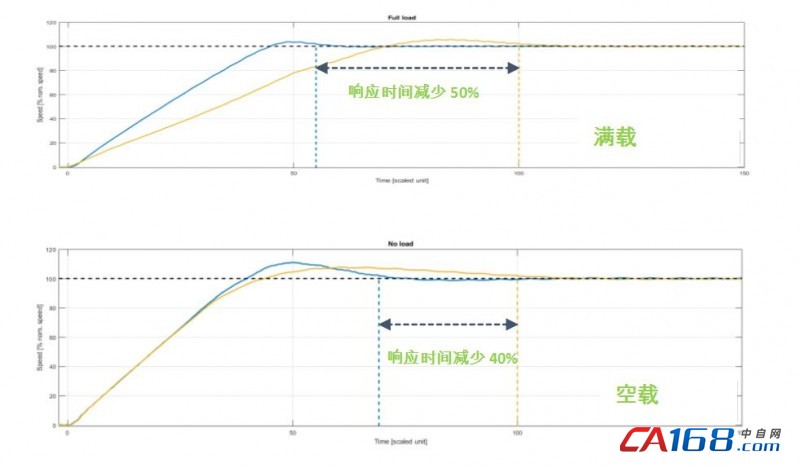
图4 传统矢量控制与AEMC控制响应时间对比图
4.采用AEMC算法的ATV930变频器在无溶剂复合机上的应用
4.1. 无溶剂复合机系统介绍
无溶剂复合机,是采用无溶剂型胶黏剂将两种或多种基材复合在一起的一种方法,又称反应型复合。无溶剂复合的适用范围十分广泛,其环保,卫生,高效的特点,尤其适用于食品药品包装行业。可复合的基材主要有BOPP,PET,Nylon,CPP,PE,VMPET,VMCPP,PVC,铝箔,纸张等等。基材适用厚度一般在7μm-120μm。
无溶剂复合机的电控系统主要由可编程逻辑控制器(PLC)、变频器、张力传感器等设备构成,其系统框图如图5所示。PLC完成整个系统的速度给定和扭矩给定。收卷变频器根据PLC给定的转矩参考值输出对应的扭矩。
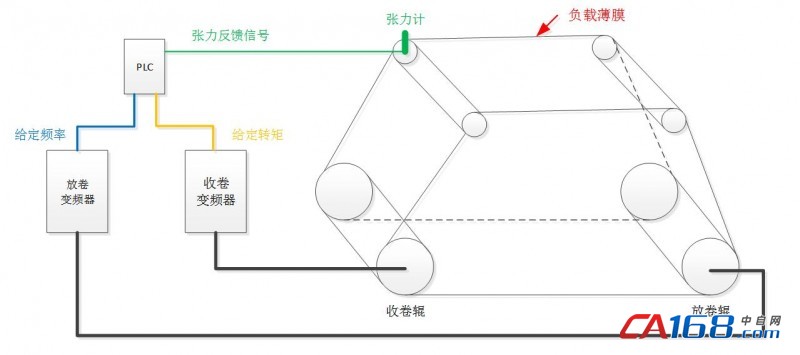
图5 无溶剂复合机系统框图
该系统收卷工艺在PLC内部采用使用张力闭环控制模式,其中PLC的模拟量口采集张力传感器的张力信号作为张力反馈量,再通过PLC内部的PID控制模块稳定系统张力,经内部的计算后将扭矩给定值输出给收卷变频器,收卷变频器控制电机输出对应的扭矩和控制系统张力,从而构成张力闭环系统。
4.2.变频器转矩输出精度的影响
在无溶剂复合机运行过程中,系统所需的张力值变化范围很大。在刚开始运行时,收卷部分负载较小,需要的系统张力值仅为电机额定转矩的2%-5%;至后期时收卷部分负载又很重,系统张力值甚至达到电机额定负载的90%-100%。考虑到负载的变化特性,系统的PID功能需要调试至相对缓慢,用以应对负载的逐渐变化,否则易导致系统张力波动较大,影响薄膜质量。
在此应用情形下,在无溶剂复合机启动初期,对于变频器的转矩精度要求必须控制在小于1%以内。且在此扭矩给定下,也要求变频器能够运行足够高的频率已响应系统速度。
如图6所示,在系统加速过程中,考虑到PLC的转矩给定值有一个加速过程,及变频器力矩输出克服系统摩擦力的阈值,故在给定变频器的转矩小于系统摩檫力时,电机不转。这导致系统运行初期收卷电机速度低于放卷速度。随着张力传感器反馈值和设定值的误差不断增加,PLC内部经转矩闭环PID输出到变频器的扭矩给定值也不断增加,最终给到一个能够能够让系统张力稳定的扭矩给定值。从系统运行至张力稳定的时间称为响应时间。
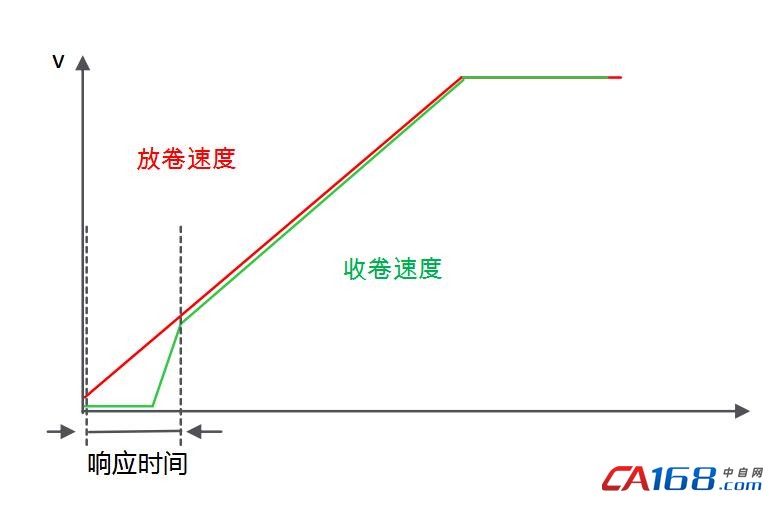
图6 响应时间定义示例图
在此加速阶段,对变频器的扭矩精度要求小于1%。否则会导致系统张力值变动大,从而使无溶剂复合机所加工的薄膜脱落或者拉断。
图7为客户使用标准矢量控制时,通过变频器的安装调试软件Somove读出的变频器运行曲线。如图7所示,其中输出转矩OTR(绿色曲线),电机运转频率RFR(枣红色曲线),未滤波的输出转矩SOTR(黄色曲线),PLC给到变频器的张力给定值AIV1(褐色曲线)。可以从图7中看到张力计转矩波动较大,在实际运转过程中,薄膜出现了松落及过度拉伸的情况。
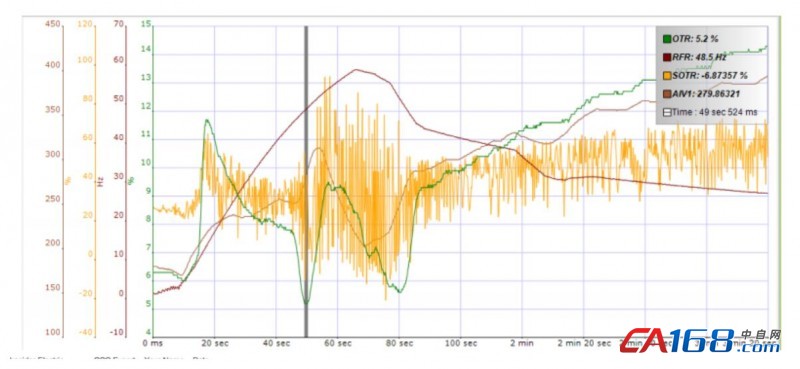
图7 传统矢量控制Somove波形图
图8为从PLC侧所读取的系统运行曲线,从实际张力值(淡蓝色曲线)可以看到系统的实时张力值在启动之后几乎降低为0。即薄膜已经松落。
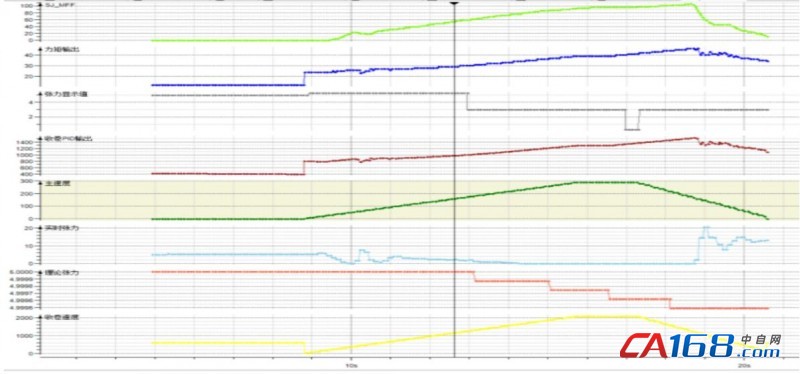
图8 传统矢量控制PLC采样信号图
4.3.采用AEMC算法的ATV930变频器的效果
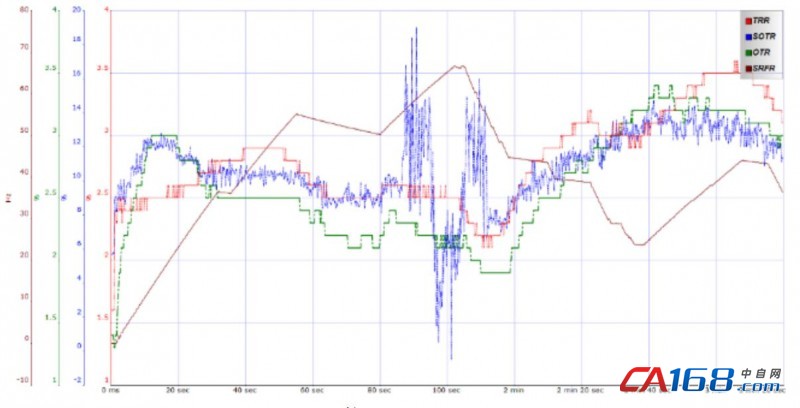
图9 AEMC控制Somove波形图
如图9所示,在同样的负载情况下,使用AEMC及做相应的参数设置之后,我们可以看到输出转矩(OTR,图9中绿色曲线)和给定转矩(TRR,图9中红色曲线)误差小于0.5%额定转矩。实际运转中薄膜运转正常,没有出现薄膜松落及拉断的现象发生。
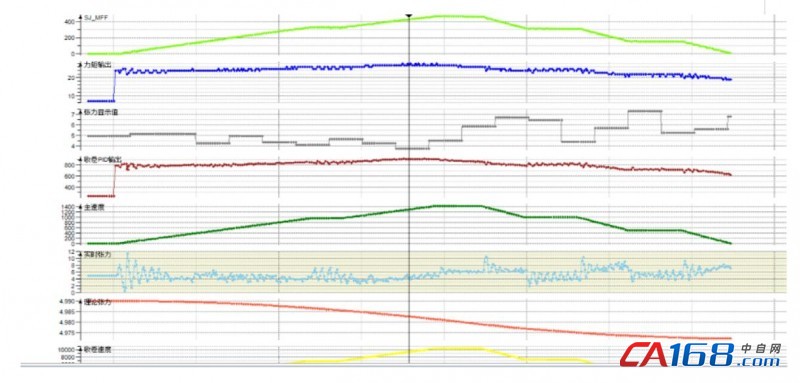
图10 AEMC控制PLC采样信号图
与此同时在PLC端观测张力计实际反馈值(图10中淡蓝色曲线)时,可以看出张力实际波动较小,也没有出现张力值跌落到0的情况。
5.结语
在张力控制收放卷工艺中使用施耐德变频器第五代矢量控制算法(AEMC),可以将电机转矩输出精度控制在电机额定转矩1%以内,结合张力控制中的张力计方案,可以显著提高成品质量。在应用于无溶剂复合机实际产品中,通过使用AEMC算法,解决了使用前代算法时存在的松膜或断膜问题。提高了产品的综合竞争能力。
参考文献:
[1]Schneider Electric. Altivar Process ATV900 Variable Speed Drives for Asynchronous and Synchronous Motors Programming Manual[Z]. 06/2021.
共0条 [查看全部] 网友评论