摘要:机器人自动柔性搬运系统具有很高的效率和产品质量稳定性,柔性较高且可靠性高,结构简单,便于维护,可以满足不同种类产品的生产,对于重型汽车生产厂家来说,可以很快进行产品结构的调整和扩大产能,同时大大降低了产业工人的劳动强度,具有广泛的应用前景。
关键词:自动柔性搬运 定位 视觉定位技术
引 言
本文以一个机床上下料应用实例,介绍机器人在智能化机床上下料应用中所涉及到的新技术,以及机器人在机床上下料领域中的应用前景。着重描述了机器人对无夹具定位工件的自动柔性搬运(2D视觉技术)以及3D视觉定位技术。
前 言
桥箱类零件生产具有精度高、加工工序多、形状复杂、重量重的特点,为提高加工精度及生产效率,各重型汽车生产厂纷纷采用数控加工中心来加工此类的零部件。使用数控加工中心加工工件时,要求工件在工作台上具有非常高的定位精度,且需要保证每次上料的一致性。由于人工上料这类的工件具有劳动强度高、上料精度不好控制等缺点,现在正逐步被工业机器人或专机进行上下料所取代。工业机器人的应用具有重复定位精度高,可靠性高,生产柔性化,自动化程度高等无可比拟的优势。与人工相比,能够极大地提高生产效率和产品品质;与专机相比,具有可实现生产的柔性化,投资规模小等特点。机器人智能化自动搬运系统作为减速器壳体加工的重要生产环节,已经在国内重型汽车厂内取得成功的应用,但在国内应用还不广泛。在国家经济建设飞速发展的进程中,重型载重汽车的生产能力及生产力水平亟待有一个质的飞跃,而工业机器人即是提升生产力水平的强力推进器,具有广阔的市场前景。
现场布局
现场布局
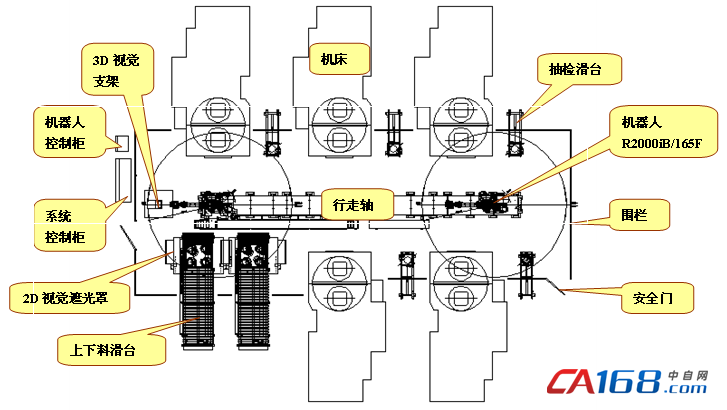
项目描述
该系统使用1台机器人完成服务5台机床进行上下料的作业,系统描述如下:
1台FANUC R-2000iB/165F机器人:安装于行走轴上,实现整个系统的上下料动作。
1个机器人手爪:基于机器人专用手爪单元开发的手爪,非常适用于工件一致性不好的
使用情况,并有较高的定位精度和抓持稳定性,定位精度高、耐用性好、维护简单的优点。
1个长11m的行走轴:在行走轴导轨上安装一台工业机器人,最大运动速度为1.5米/秒,
使用FANUC伺服电机驱动,具有重复定位精度高、响应速度快、运行平稳、可靠等特点,
并专门设计了防尘罩,保护导轨、直线轴承以及齿条等运动部件,大大提高了可靠性和使用
寿命。在实际应用中,导轨安装于两条生产线机床的中心线上,所安装的工业机器人运动范
围完全覆盖5台机床以及上下料滑台区域。从而实现了1台机器人服务5台机床进行上下料作
业。
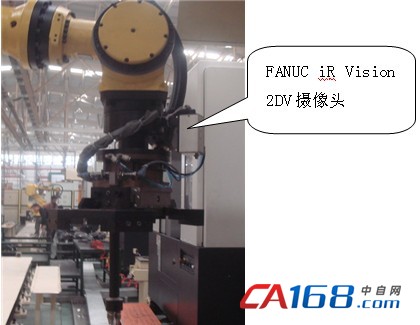
手爪
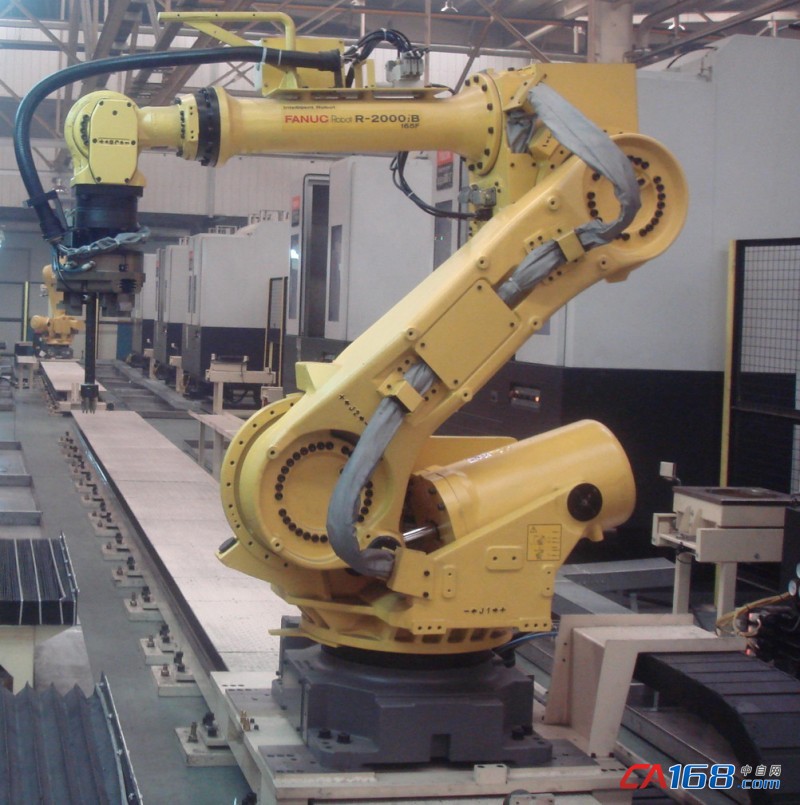
行走轴
2台上下料滑台:每个上下料滑台上有4个托盘,每个托盘分别可以存放一个工件。实现待加工工件的上料,以及加工完成工件的下料。在该系统中,由于使用了视觉技术,因此上下料滑台无需工件的定位装置。
FANUC iR Vision 2DV视觉系统:该视觉系统由一个安装于手爪上的2D摄像头完成视觉数据采集。该视觉系统作为待加工工件准确抓取的定位方式,省去通常为满足机器人的准确抓取而必须采用的机械预定位夹具,具有很高的柔性,使得在加工中心上可以非常容易地实现多产品混合生产。
FANUC iR Vision 3DL视觉系统:该视觉系统由一个安装于地面上的3D Laser Sensor完成视觉数据采集。该视觉系统解决了定位面有偏差的工件上料位置变化问题。由于待加工工件为毛坯件,机器人抓取工件后,上料的定位孔位置会发生变化,甚至工件上料时的平面度也有变化。该技术可以自动补偿位置变化,实现高精度上料。
系统流程
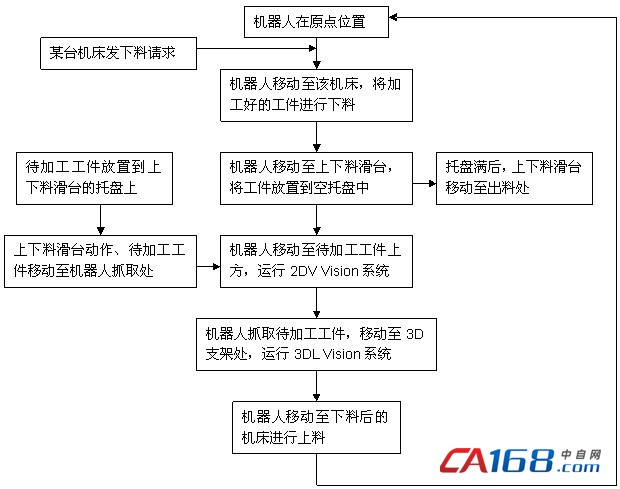
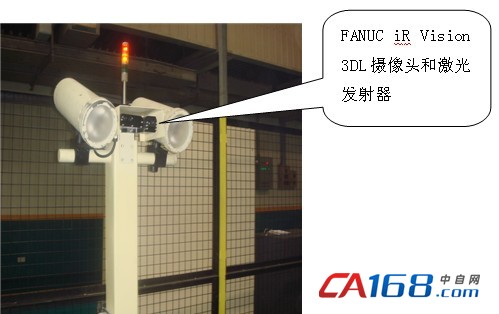
3DL视觉支架
5台抽检滑台:针对每台机床有一个抽检滑台,实现随时对该机床工件加工工件质量的检测。
电气控制系统:运用人机界面对整个系统的运行状态进行监控,采用三菱Q系列PLC控制器,并使用工业现场总线实现系统中实时和非实时数据的传输,具有高度可靠性和可维护性。安全设备采用门开关,作为机器人工作区域的安全防护,完全做到人机隔离,确保系统在自动运行中的人员安全。
该套设备的应用极大地提高了产品的质量稳定性,节省了大批人工,提高了企业的自动化水平,减少了企业的劳动力成本支出,提高了产品的市场竞争力。
系统流程
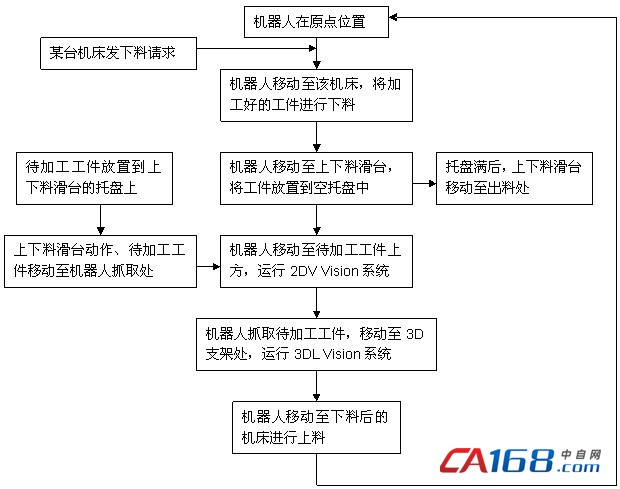
无夹具定位工件的自动柔性搬运
随着国家和社会的进步,对机械产品的加工也提出了更高的要求,促进了机床加工技术的不断提高,同时对机床在加工过程中工件的上下料方式也提出了更高的要求,现代机械产品的加工具有自动化程度高、安全文明、环保性好(噪音小)、实用性强等显著特点和优势,以机器人在机械加工中的自动化应用为代表,在各个加工领域的应用越来越广,将成为现代机械加工的主流辅助设备。
在国外,在机械产品的加工中使用机器人已经非常普遍,它具有速度快、柔性高、效能高、精度高、无污染等优点,是一种非常成熟的机械加工辅助手段。机器人对无定位工件的自动柔性搬运系统的工作原理,就是利用高清晰摄像头(vision系统)实现对无定位工件的准确位置判断,在机器人收到信号后,机器人装上为工件定制的专用手爪去可靠的抓取工件,在与机床进行通讯得到上料请求后,最终完成机床的上下料。在各种机械加工行业中该系统应用广泛。使用机器人对无夹具定位工件的自动柔性搬运系统可以使生产流水线更加简单易于维护,并大幅度降低工人的劳动强度,效率和柔性又比较高。该系统结构简单、安全文明、无污染,能在各种机械加工场合进行应用,满足了高效率、低能耗的生产要求。在国内的机械加工,目前很多都是使用专机或人工进行机床上下料的方式,这在产品比较单一、产能不高的情况下是非常适合的,但是随着社会的进步和发展,科技的日益进步,产品更新换代加快,使用专机或人工进行机床上下料就暴露出了很多的不足和弱点,一方面专机占地面积大,结构复杂、维修不便,不利于自动化流水线的生产;另一方面,它的柔性不够,难以适应日益加快的变化,不利于产品结构的调整;其次,使用人工会造成劳动强度的增加,容易产生工伤事故,效率也比较低下,且使用人工上下料的产品质量的稳定性不够,不能满足大批量生产的需求。使用机器人自动柔性搬运系统就可以解决以上问题,该系统具有很高的效率和产品质量稳定性,柔性较高且可靠性高,结构简单更易于维护,可以满足不同种类产品的生产,对用户来说,可以很快进行产品结构的调整和扩大产能,并且可以大大降低产业工人的劳动强度。在这种趋势下,对机器人自动柔性搬运系统的需求会大量增加。
FANUC iR Vision 2DV视觉系统主要是通过视觉系统软件设置,建立视觉画面上的点位与机器人位置相对应关系。对工件进行视觉成像,与已标定的工件进行比较,得出偏差值,即机器人抓放位置的补偿值,实现机器人自动抓放。该技术实现了机器人在无夹具定位工件情况下的自动柔性搬运。在该上下料系统中,待加工工件形状复杂,用夹具进行定位非常复杂,同时不利于以后同类新产品的扩展。在应用了FANUC iR Vision 2DV视觉系统后,待加工工件只需放置于上下料滑台无定位装置的托盘上,实际情况为待加工工件可以在托盘上移动正负2厘米以及旋转正负30度。这样大大减少了在上下料滑台上的设计工作,保证了系统的扩展功能。
原理:选一个待加工工件作为初始工件,通过2DV视觉软件对该工件在摄像头中的画面点位与机器人示教点位的关系进行标定,同时完成初始工件的特征标定。示教完成的抓取程序为初始工件初始位置的抓取位置,此时工件抓取偏差值为零。当工件平移或者旋转后,位置与初始工件的位置发生变化。通过2DV软件,机器人能够计算出位置变化量X、Y、R。机器人把该偏差值存入位置寄存器PR[]中。此时机器人可以通过把偏差值PR[]补偿到初始抓取位置来实现工件的抓取。

2DV视觉布置
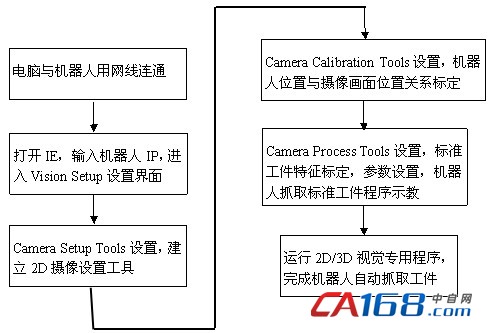
2DV视觉系统操作流程
补充:在该上下料的应用中只有一种工件,当有多种工件时,2DV视觉系统可以根据不同的工件进行多次特征标定,实现多种工件之间的切换调用。大大提高了系统的可扩展性,柔性度高。
3D视觉定位技术
应用于机器人上料至机床。
摄像头安装位置:固定在3DL视觉支架上。
该技术解决了定位面有偏差的工件上料位置变化问题。由于加工工件为毛坯件,机器人抓取工件后,上料的定位孔位置会发生变化,甚至工件上料时的平面度也有变化。对于此种情况,在没有 3DL视觉系统的情况下,机器人是无法实现对工件的准确上料。
原理:选一个毛坯件作为初始工件,通过3DL视觉软件对该工件在摄像头中的画面点位与机器人示教点位的关系进行标定,同时完成初始工件的特征标定。示教完成的上料程序为初始工件初始位置的上料位置,此时工件上料偏差值为零。当抓取其它毛坯件后,定位孔位置以及工件的平面度发生变化。通过3DL软件,机器人能够计算出位置变化量X、Y、Z、W、P、R。机器人把该偏差值存入位置寄存器PR[]中。此时机器人可以通过把偏差值PR[]补偿到初始上料位置来实现工件的上料。
软浮动功能(Soft Float)
结 论
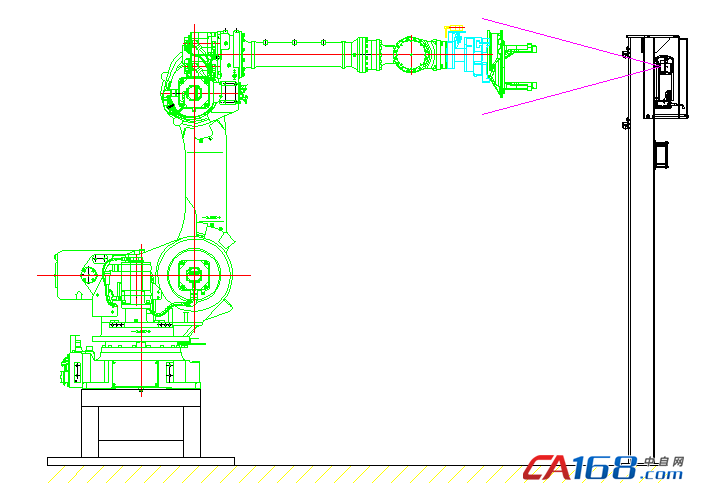
3DL视觉布置
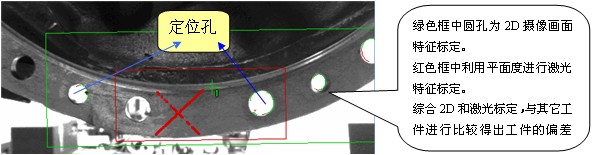
3DL视觉标定画面
补充:2DV是通过摄像头计算平面变化量,3DL是通过摄像头和激光综合计算空间变化量,实际上是2DV与激光技术的综合应用。该技术的应用大大增加了系统设计的可行性,尤其是在遇到定位面有偏差的工件设计时。
软浮动功能(Soft Float)
应用于工件抓取和机器人机床上、下料步骤。
该项目中机器人手爪抓取待加工工件位置在毛坯面,各个毛坯件抓取位置与定位孔位置都有差异。虽然有2DV视觉补偿,但是毛坯面不能作为特征量,导致在机器人手爪抓取工件的位置在不停的变化,机器人无法补偿此偏差。以下是由于毛坯面与定位孔位置变化带来的问题:
a. 工件在托盘内,机器人抓取后,由于毛坯面带来的偏差,导致工件在手爪抓取时有移动,偏差大时与托盘有摩擦;
b. 机器人从机床下料时,由于毛坯面带来的偏差,导致手抓不能完全贴合毛坯面,即使强硬贴合上,在工件脱离定位销时会有严重的摩擦,导致碰撞报警;
说明:软浮动功能在开启后,机器人可以受外力改变姿态,改变大小可以通过参数设置。手爪在抓取毛坯件时可以根据毛坯面改变姿态,达到完全贴合,避免碰撞和摩擦。
补充:该项目中,工件定位孔与机床定位销(锥形)之间的配合精度达到0.01毫米。机器人本身的重复精度大于0.01毫米,导致工件上料位置偏差。此时应用软浮动功能,机器人抓取工件运行到定位销锥度部位,由机床夹具夹紧,机器人通过软浮动移动至上料位置,实现上料过程。
结 论
随着国家经济的快速增长,重型载重运输汽车的需求在不断地扩大,为满足市场的需求,各重型汽车厂在不断地积极开发新产品,并扩大原有产能。使用机器人服务加工中心组成柔性加工生产线的自动化方式逐步得到广泛采用,从而在提高生产效率、减少人工成本、保障作业安全、提高生产品质等方面起到了显著作用。机器人自动柔性搬运系统具有很高的效率和产品质量稳定性,柔性较高且可靠性高,结构简单,便于维护,可以满足不同种类产品的生产,对于重型汽车生产厂家来说,可以很快进行产品结构的调整和扩大产能,同时大大降低了产业工人的劳动强度,具有广泛的应用前景。
共0条 [查看全部] 网友评论