四. 软件实现与现场结果
4.1 系统结构
基于LabVIEW的倒车自动刹车系统主要分为两个部分:
4.1.1 数据采集(下位机部分)
依据前文所述的系统模块可将数据采集分为两个部分。在测距模块中,驱动NI 9264模拟输出产生周期为30ms的40kHz超声波激励信号,通过NI9205接收反射波信号,并利用Labview的脉冲探测函数计算超声波的传播时间,从而计算出车—障碍物的实时距离。在刹车控制模块中,利用NI 8473与车载CAN网络无缝连接,实现DPC与车载设备的数据交互。
4.1.2 数据处理(上位机部分)
数据传输及数据处理(即DPC)是基于LabVIEW2010平台开发的。刹车控制模块的数据传输通过LabVIEW2010平台下的CAN模块与车载CAN网络实时通信,获取实时车速及EVB实际压力值的CAN报文,并通过相同的CAN通道发送EVB期望压力值报文。DPC使用LabVIEW平台中的“生产者—消费者”模型对数据采集部分返回的大量实时数据按一定周期进行处理,以此减少系统耗时从而加快程序处理的速度并提高系统的响应速度。通过LabVIEW状态机结构对车辆实时状态进行特征参数提取,以此确定车辆在倒车行进过程中的加速状态、匀速状态以及减速状态,并针对不同状态进行相应的控制。
4.2 控制软件界面及功能
数据传输、处理与控制软件界面主要包括3大功能模块:参数配置模块、功能验证模块以及报表输出模块。界面如图12、13、14所示。
图12 初始界面
图13 参数配置界面
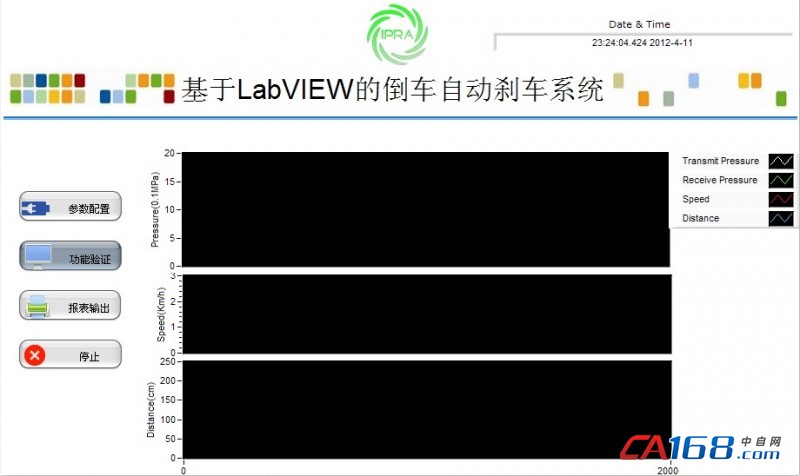
图14 功能验证界面
4.3.1 实时数据展示
在参数配置界面对Fuzzy—PI算法的特征变量的相关参数进行配置,继而通过功能验证模块进行实车测试效果。通过对测试数据的综合分析,实时修改算法的相关参数值。图15即为在实车验证状态下的实时数据曲线图。
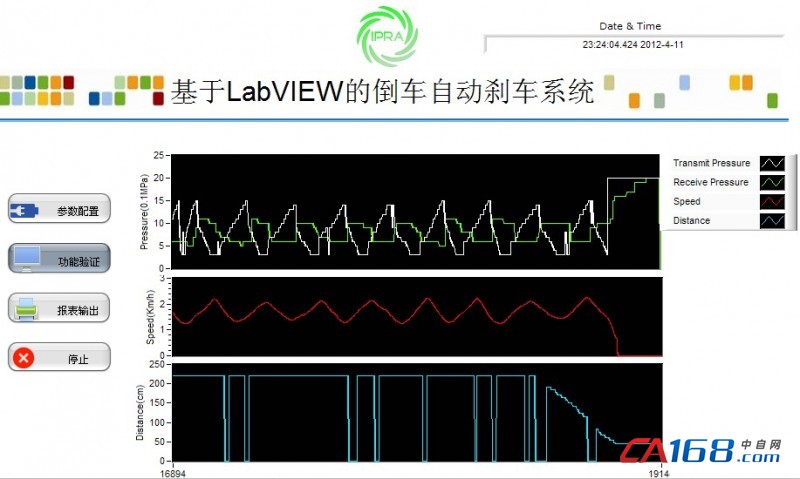
图15 基于LabVIEW的倒车自动刹车系统的实时曲线
报表输出功能将速度轨迹及加速度轨迹以Excel的格式输出,其结果如图16、17所示。
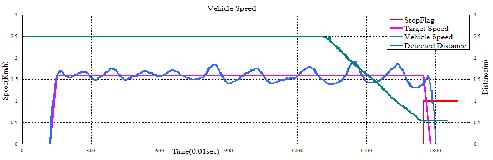
图16 基于LabVIEW的倒车自动刹车系统的控制结果
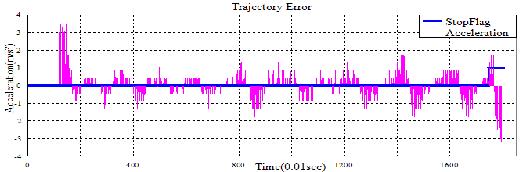
图17 基于LabVIEW的倒车自动刹车系统的加速度轨迹
4.3 现场成果
本系统安装于长安志翔CV8上,车载CAN网络通过NI 8473与笔记本电脑上的LabVIEW平台实时通信。同时将超声波传感器安装于车后牌照正上方,并通过NI DAQ平台配置NI9269及NI9221的相关参数,从而驱动超声波传感器。图18为超声波传感器与相关数据采集设备的连接图,图19为现场时设备连接图。
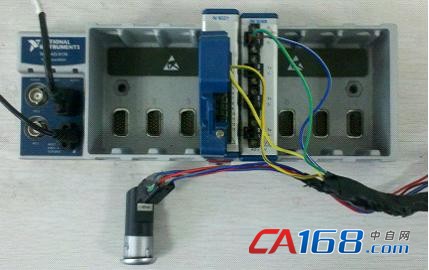
图18 超声波传感器的设备连接图
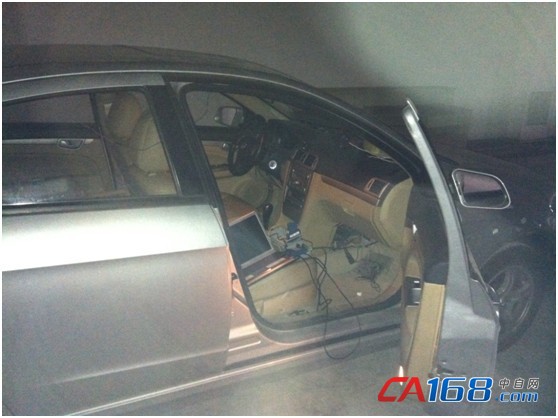
图19 现场设备连接图
五. 结论
从技术层面讲,NI DAQ平台和LabVIEW开发环境无缝连接使用户轻松的通过图形化开发环境访问底层硬件,快速建立系统原型和数据采集应用,大大降低了系统开发的技术风险。LabVIEW强大的数据采集和信号处理功能极大地节省了采集终端软件的开发时间,在NI DAQ平台和LabVIEW CAN模块的配合下使得采集终端能够实时并且高质量地完成数据采集、信号处理、数据传送和数据处理的工作,为整个系统的开发研究提供灵活、强大的底层硬件支持。
基于LabVIEW平台的倒车自动刹车系统已在长安志翔CV8上成功实现相关功能,该系统的成功开发在速度控制领域及相关辅助系统开发方面取得突破性进展。同时对长安汽车有限公司正在进行的全自动泊车系统的开发奠定夯实的技术基础。
共0条 [查看全部] 网友评论