挑战:制动控制单元(Brake Control Unit,BCU)是动车组制动控制系统的核心部件,担负着制动力计算、电空联合制动演算控制、防滑控制、空压机控制、通信、监控以及故障处理等任务。目前对BCU的检测诊断集中于BCU设备整体功能检测,一旦设备存在故障,无法定位故障电路位置,最终可能导致整个设备损坏,并增加维修成本甚至危及动车组的可靠安全稳定运行。因此研制开发高集成度、自动化、智能化单板故障测试与诊断系统,用于大批量产品的出厂检测和定期维护维修,具有重要的实际意义和经济价值。
应用方案:本试验台设计实现对动车组制动控制单元的单板测试,可实现电源板、接口板、防滑板、CPU板、通信板的功能测试。本测试系统采用自上向下逐层设计的方法与自底向上逐层实现的方法相结合的技术解决方案。首先在明确被测试对象特征和测试任务的前提下,自上而下分析系统总体结构的层次模型,建立系统的总体设计框架,根据设计目的及功能的不同,进行分模块设计和软硬件划分,对测试系统的软、硬件进行总体设计。其次,在测试系统实现过程中,在搭建测试系统的基本应用框架的基础上,完成对基本数据结构的定义及各模块之间的接口定义,然后由基本模块开始,完成对关键模块的设计,再逐步完成其它模块的设计,最后设计完成整个测试系统。
使用的产品:
LabVIEW 2009 软件开发平台
PXI-1045机箱
PXI-8108嵌入式控制器
PXI-4070数字万用表
PXI-2503矩阵继电器开关
PXI-2566大电流继电器开关
PXI-2570多通道通用继电器开关
PXI-6528数字量输入输出模块
PXI-6723模拟量输出模块
PXI-6220模拟量输入模块
PXI-6602计数器/定时模块
PXI-2575开关模块
以及配套的接线盒和线缆
正文:
引言
一、近年来高速铁路迅速发展,高速列车运行的安全性备受人们的关注,因此高速列车制动系统的可靠性显得更为重要。制动控制单元是高速动车组制动控制系统的核心部件,担负着制动力计算,电空联合制动演算控制、防滑控制、空压机控制、通信、监控以及故障处理等任务。目前对BCU的检测集中于BCU设备整体功能检测,一旦设备存在故障,无法定位故障电路位置,最终可能导致整个设备损坏、增加维修成本等后果。因此研制开发高集成度、自动化智能化单板故障测试系统,用于大批量生产产品的出厂检测和维护维修,并应用电路板故障诊断技术对BCU制动控制单元进行单板测试及故障电路定位有重要的现实意义。
针对BCU大容量的数据采集工作,以及铁路高可靠性的测试需求,采用传统基于分立测量与数据处理设备的将受到数据传输速率、设备占地面积以及测试环境等条件的制约。本试验台采用NI公司基于PXI总线的数据采集系统,通过PXI嵌入式控制器配合数据采集板卡,通过软件控制灵活的对各数据采集板卡进行功能配置,最大程度实现硬件的复用,极大地简化了系统结构,并提升数据传输速度,整个测试系统相对于整机测试系统具有更高的数据吞吐量和测试速率。
二、BCU单板检测系统的设计背景和开发理念
制动控制单元包括CPU板、接口板、防滑板、电源板和通信板五块电路板。图1是BCU的工作原理结构图,通过司机控制器、列车传感器和列车通信网络等传输的数据信息和指令信息,BCU进行复杂的制动计算和防滑计算,输出列车当前需要的制动力,并驱动中继阀和防滑阀,控制制动风缸完成列车制动。
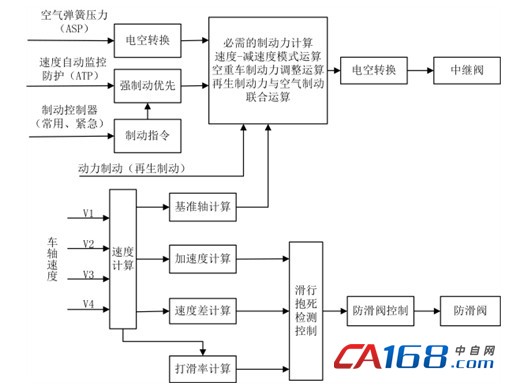
图1 制动控制单元工作原理示意图
单板测试试验台根据人机交互界面输入信息,模拟传感器和列车网络传输的数据,模拟制动过程,经过运算后与数据采集系统检测到的数据进行比对,验证BCU各单板工作状态。主要包括三个方面的任务:首先是根据主控制器PXI-810的控制指令,数据输出板卡输出模拟量、数字量、PWM等信号至BCU各电路板,提供电路板工作的原始激励型号;其次是进行模拟运算,计算当前状况下BCU单板各路信号的输出值;最后还要对BCU单板输出进行高精度的采集,完成数据的比对、判别和存储。
系统设计主要遵循以下几个方面理念:
1. 充分发挥虚拟仪器技术的优势,采用软件配置代替硬件资源,对数据采集板卡硬件资源达到资源利用最大化;
2. 整体规划单板测试试验台软硬件资源配置,将测试测试内容划分为导通测试、特性测试、电压测量、模拟量输出回路测试、PWM频率/脉宽测试等10大类17个测试项,对不同电路板相同测试项目可合并为一组进行测试,以便硬件资源的重用和测试速度的加快;
3. 测试实现自动测试和手动测试,有条件的最大程度的向用户开放底层硬件控制权,方便二次开发;
4. 利用NI公司提供的基于Intel酷睿双核处理器T9400的高性能处理器主板,实现多线程操作,加快测试速率;
5. 测试智能化,系统支持测试数据保存打印,测试报告自动生成等辅助功能;
6. 采用触摸屏作为人机界面,界面丰富友好。
三、BCU单板测试系统的整体设计
在组建BCU自动测试系统时,必须考虑硬件平台的通用性与扩展性。整个平台能适应被测设备本身状态的变化,同时在现有硬件资源的基础上具有较强的扩展升级能力,并满足系统的小型化需求。本系统采用内嵌式控制方式以及3U的PXI模块,数据采集单元、信号模拟单元均基于PXI总线,并在PXI机箱内实现,这是整个自动测试系统的核心。
本系统采用内嵌式控制方式以及基于PXI总线的3U PXI数据采集模块,数据采集单元、信号模拟单元均在PXI机箱内实现。系统采用的PXI数据采集板卡及功能如下表所示(继电器、控制器除外)。
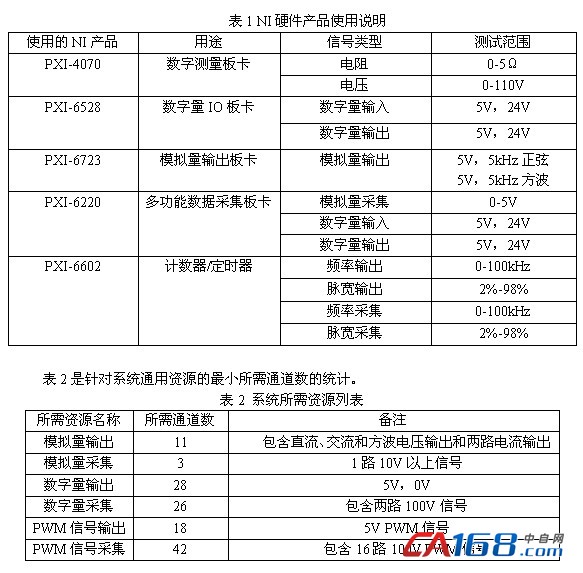
3.1 硬件的总体设计
本系统采用PXI总线,并引用PXI嵌入式工控机。在硬件资源方面采用基于PXI总线的功能强大的模块化虚拟仪器,充分发挥了PXI总线的优势,从而为电路板进行准确、快速的测试提供硬件保障。测试系统主要由以下几部分组成:主控单元主要对信号进行处理和分析,信号输出部分是给被测板提供激励信号,信号采集部分是采集被测板卡的输出信号,信号调理板是对信号进行调理及接口转换,电源部分是给被测试板卡、数字板卡及转接板供电。系统总体设计结构如图2所示。
本系统主要包括电源模块,五块被测板卡,一块转接板,一个PXI总线机箱,一个触摸液晶显示器和一台打印机等。被测板卡通过调理板卡与PXI总线机箱里的各种采集、输出、测量板卡进行连接,上层软件采用LABVIEW进行编程,实现系统的自动化测试,触摸液晶显示器是人机交互界面,打印机可以将测试结果进行打印输出。
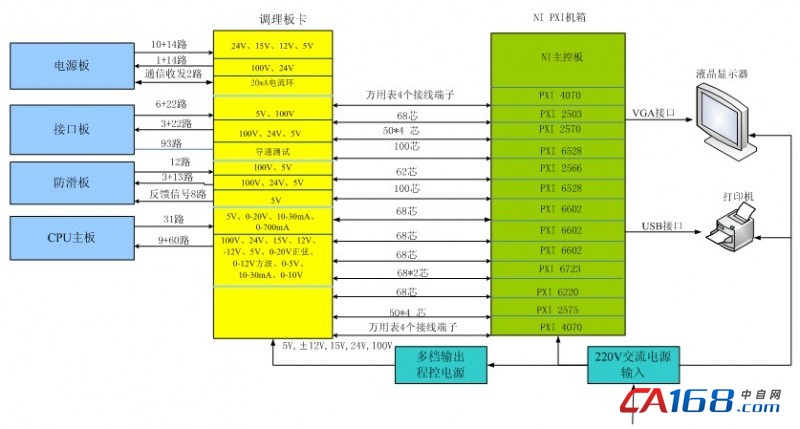
图2 BCU单板测试系统结构图
3.2 软件的总体设计
测试系统的参数设定、仪器配置、测试激励的产生、响应数据的采集、测试结果的判断、故障定位和报表生成等,都是在系统软件的控制下完成的。本测试系统将动车组制动控制单元的检测细化到电路板级,本测试系统的软件设计遵循模块化设计原则,采用LabVIEW开发环境进行编程,采用软件编程方式极大限度的对硬件资源进行配置和使用,使系统的通用型、可重用性以及可拓展性得到极大的提高,设计了丰富的人机交互界面,保证试验操作直观简单,并且能实时显示测试数据、定位故障回路。
测试软件主要由电路板自动测试模块、测试信息维护模块、人机交互模块等三个模块构成,设计了包括测试过程管理控制软件、测试子程序以及数据管理等子程序,并可自动生成报表,便于查询与打印。软件主要功能模块示意图如图3所示。
为提高系统的兼容性和可拓展性,本实验针对测试过程中的数据流设计了详细的数据维护系统。用户可以根据测试需求,通过主控计算机对测试数据进行读取、存储、分析,并生成测试报表及打印;用户也可以登陆系统,添加或删除相关测试信息,对测试数据进行维护和修改。
测试系统的参数设定、仪器配置、测试激励的产生、响应数据的采集、测试结果的判断、故障定位和报表生成等,都是在系统软件的控制下完成的。本测试系统将动车组制动控制单元的检测细化到电路板级,本测试系统的软件设计遵循模块化设计原则,采用LabVIEW开发环境进行编程,采用软件编程方式极大限度的对硬件资源进行配置和使用,使系统的通用型、可重用性以及可拓展性得到极大的提高,设计了丰富的人机交互界面,保证试验操作直观简单,并且能实时显示测试数据、定位故障回路。
测试软件主要由电路板自动测试模块、测试信息维护模块、人机交互模块等三个模块构成,设计了包括测试过程管理控制软件、测试子程序以及数据管理等子程序,并可自动生成报表,便于查询与打印。软件主要功能模块示意图如图3所示。
为提高系统的兼容性和可拓展性,本实验针对测试过程中的数据流设计了详细的数据维护系统。用户可以根据测试需求,通过主控计算机对测试数据进行读取、存储、分析,并生成测试报表及打印;用户也可以登陆系统,添加或删除相关测试信息,对测试数据进行维护和修改。
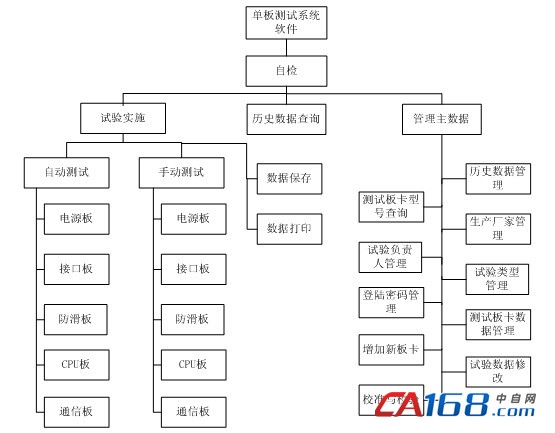
图3 软件功能流程
四、试验台开发实现及成果展示
下面从模拟量测量和PWM量测量两个方面,详细论述利用NI公司PXI数据采集系统以及LabVIEW图形化开发平台开发BCU单板测试过程。
4.1 模拟量测量
模拟量测量包括模拟量输出、模拟量采集两个硬件驱动,以及软件滤波三个重要环节。模拟量输出包括0-10V正弦波和方波、0-10V直流电压及10-30mA电流。采用NI公司PXI-6723模块以及相应V/I转换模块完成模拟输出。模拟量测试包括0-20V电压、10-30mA电流、0-700mA电流,采用PXI-6220板卡,并且配合相应的传感器、调理电路完成模拟量采集。模拟量输出及采集功能框图如图4所示:
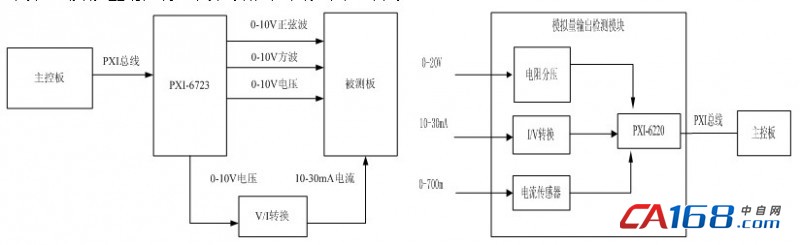
图4 模拟量输出及采集功能框图
在测量CPU板EP电流输出时,激励信号需要模拟列车数字量输入,速度输入信号和再生反馈电压信号。且要同时提供以上输入信号,被测板EP阀才能产生EP阀输出电流。因此需要并行执行输出检测操作,检测在轴速变化过程中EP电流的输出。采用LabVIEW中提供的硬件驱动以及相关函数库,可以实现简洁的实现激励信号的并行输出以及EP电流的采集。
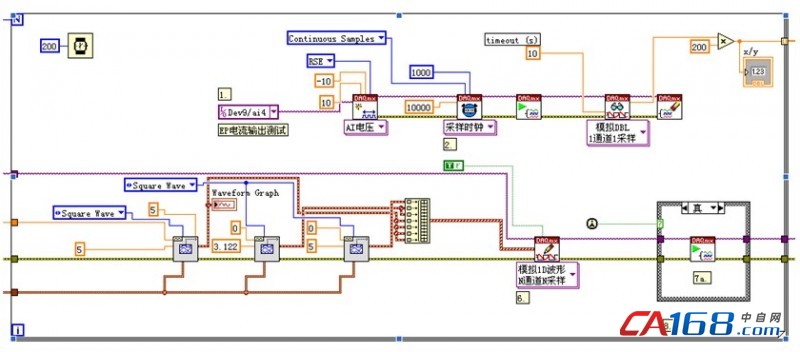
图5 模拟量输出及采集程序
由于电流传感器传输距离较长,线路会引入部分噪声,采用LabVIEW中自带的信号分析和处理工具包,设置滤波模式为低通滤波器,截止频率50Hz以防止工频及高频噪声干扰,可以有效的抑制噪声,提高EP电流测量精度。
4.2 PWM测量
PWM信号的检测过程是要先对控制继电器输入脉冲,让继电器先动作,再对防滑控制输入控制信号,同时检测其输出及反馈信号。检测PWM信号包括频率和占空比,由于在测试过程中采用的是PXI-6602采集板卡。
4.2 PWM测量
PWM信号的检测过程是要先对控制继电器输入脉冲,让继电器先动作,再对防滑控制输入控制信号,同时检测其输出及反馈信号。检测PWM信号包括频率和占空比,由于在测试过程中采用的是PXI-6602采集板卡。
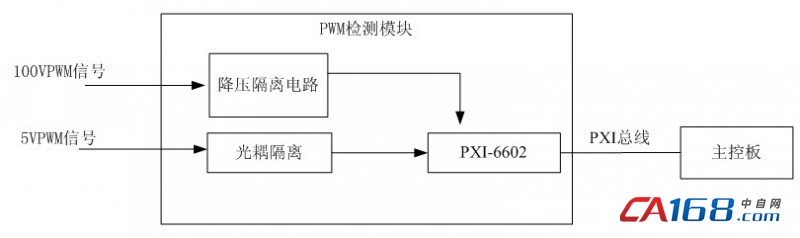
图6 PWM采集功能框图
频率采集的任务完成过程如下:
(1)开始脉冲输出任务:根据用户指定通道,生成控制脉冲;
(2)输出防滑控制脉冲任务:根据用户指定通道,生成防滑控制脉冲;
(3)脉冲检测任务:创建针对脉冲频率采集任务,将采集结果显示于前面板,结束任务;
(4)结束脉冲输出任务:结束脉冲输出,释放硬件资源;
(5)错误处理:如果测量结果出现错误或警告,弹出对话框进行提示。
程序执行图如图7所示。
(1)开始脉冲输出任务:根据用户指定通道,生成控制脉冲;
(2)输出防滑控制脉冲任务:根据用户指定通道,生成防滑控制脉冲;
(3)脉冲检测任务:创建针对脉冲频率采集任务,将采集结果显示于前面板,结束任务;
(4)结束脉冲输出任务:结束脉冲输出,释放硬件资源;
(5)错误处理:如果测量结果出现错误或警告,弹出对话框进行提示。
程序执行图如图7所示。
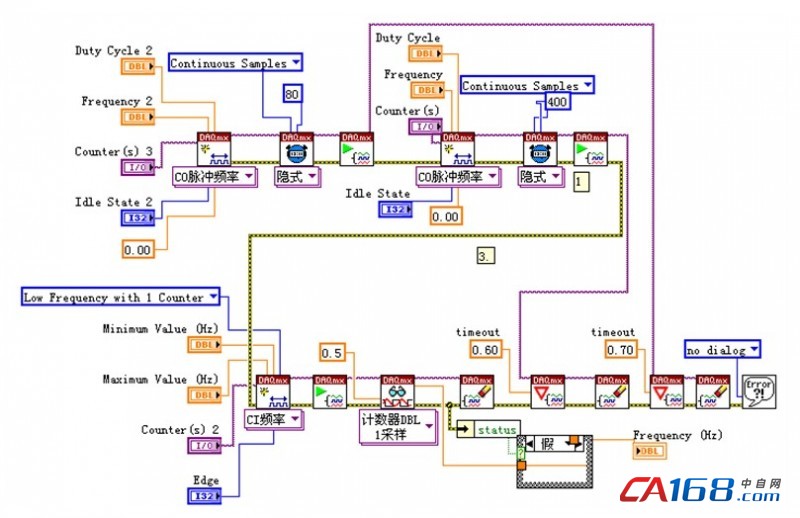
图7 防滑板PWM检测程序
4.3 人机交互界面开发
系统软件界面如图8所示:
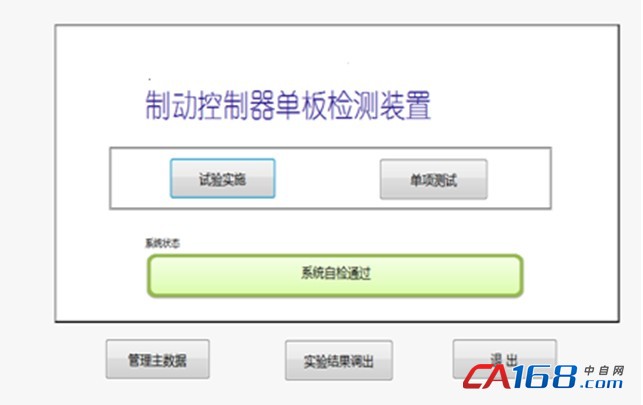
图8 单板检测系统主界面
其操作功能包括:
(1) 试验实施:进入电路板测试界面,对五类电路板进行单板测试试验;
(2) 单项测试:进入电路板硬件确认界面,对五类电路板每一项测试参数进行调整,查看试验结果。主要用于对于测试电路板个别项目的测试;
(3) 试验结果调出:查看已保存的历史数据;
(4) 管理主数据:对菜单登记项、用户信息、试验参数等进行数据管理和查看;提供查看历史数据入口;
(5) 退出:退出制动控制单元单板检测程序。
进入试验实施,系统将隐藏主界面,进入单板测试试验登记界面。试验实施界面包括试验信息登记、试验实施以及其他辅助窗口组成,可以进行四类电路板的单板测试,以及测试数据查看、保存、打印。试验登记时自动测试的必要步骤。
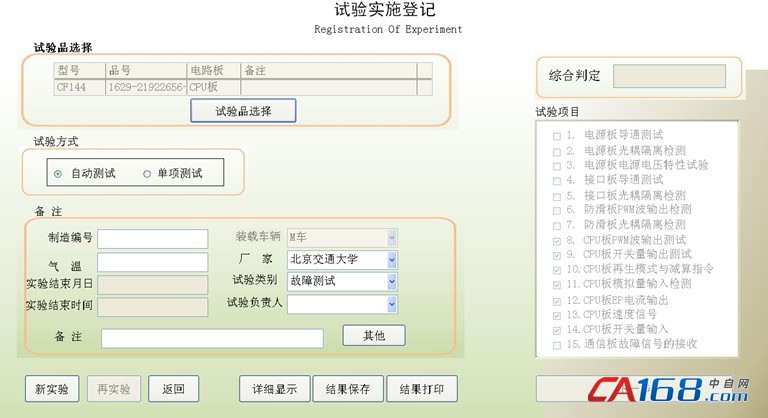
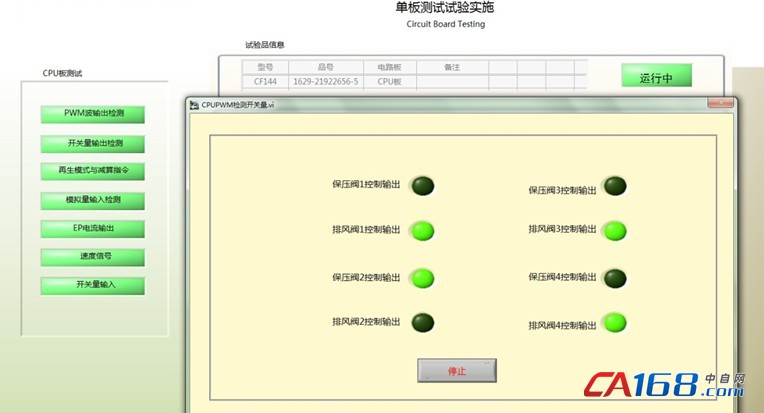
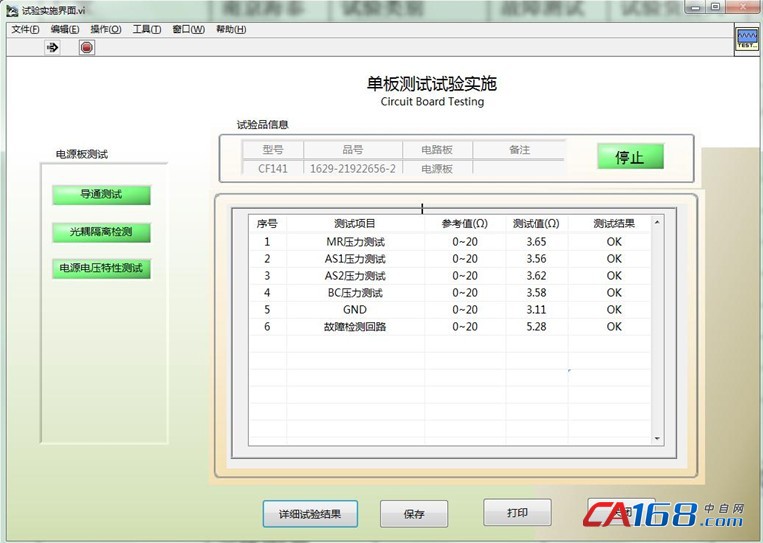
图9 自动测试界面
制动控制单元手动测试提供针对每一路测试信号的单路输入输出测试,方便用户针对某一路电路故障进行检测和调试。为用户开放了更大权限的底层硬件控制权。
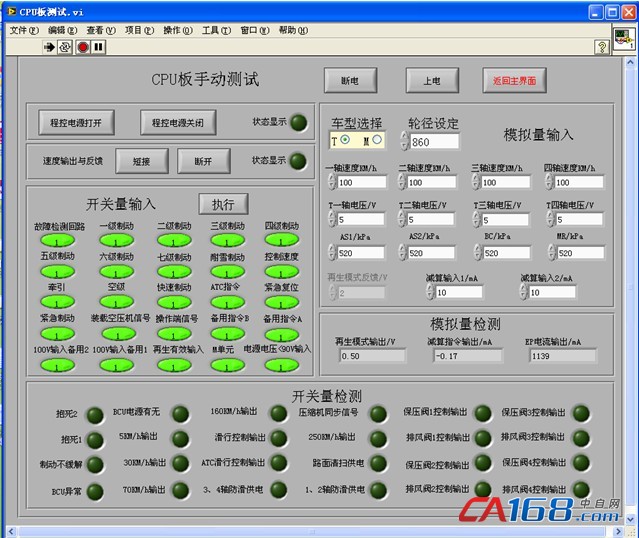
图10 CPU板手动测试前面板
系统包括了基于SQL Server的数据管理系统对历史数据和测试过程数据的数据管理系统,设计了基于多级用户权限的数据查看修改打印的管理系统。
用户在进行高级数据操作,需要进行身份验证。历史数据查询提供对以往所有测试项目的数据查询操作。
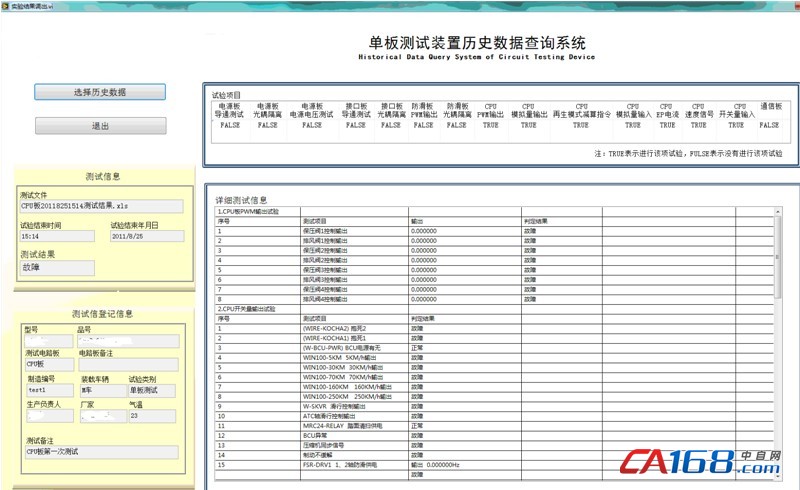
图11 身份验证及历史数据查询
4.4 试验开发架构
综上所述,对于被测电路板,由于所要测试的路数之多、功能复杂,完成测试软件的任务繁重,因此本系统对人机交互、试验测试、文件操作等采用分层结构模块化设计,由上层到下次逐步分解,并从底层到上层逐步执行,并生成对应子vi,供上层调用,下层由上层提供参数配置,并将结果数据返回给上层并进行处理。最大程度的利用LabVIEW中的相互调用实现硬件的可重用与软件的模块化。
综上所述,对于被测电路板,由于所要测试的路数之多、功能复杂,完成测试软件的任务繁重,因此本系统对人机交互、试验测试、文件操作等采用分层结构模块化设计,由上层到下次逐步分解,并从底层到上层逐步执行,并生成对应子vi,供上层调用,下层由上层提供参数配置,并将结果数据返回给上层并进行处理。最大程度的利用LabVIEW中的相互调用实现硬件的可重用与软件的模块化。
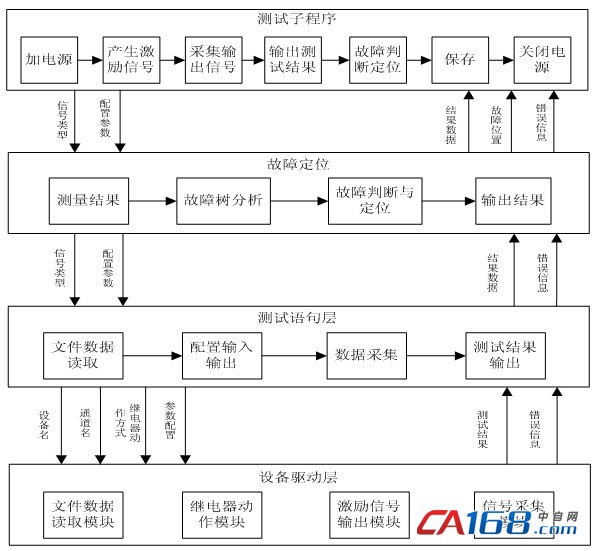
图12 子程序结构图
4.5 现场测试试验
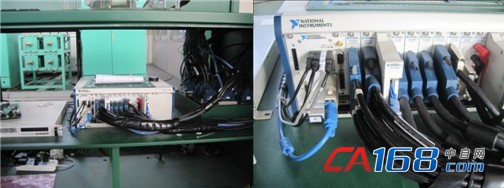
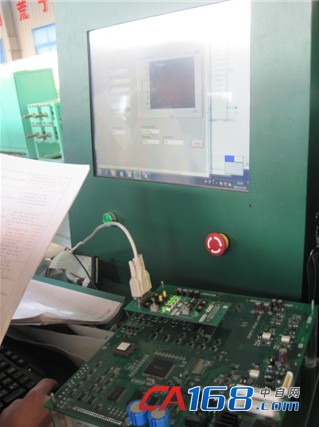
图13 现场测试图
以特性测试中CPU板EP电流测试和防滑板PWM输出测试为例,阐述制动控制单元单板测试过程和分析结果。
拖车CPU电路板在空车情况下EP电流测试结果如图14所示,对工作正常和发生故障的CPU板进行分析对比。根据制动控制单元设计要求,EP电流输出允许误差为±15mA。图14(a)所示为无故障CPU板在快速制动下制动控制单元输出EP电流;图14(b)为发生故障CPU板在快速制动下的输出EP电流;然后由手动单路测试确定是CPU板的AS1和AS2压力输入采集回路发生故障,导致输出EP电流偏低。试验结果证明了测试系统的可靠性和准确性。
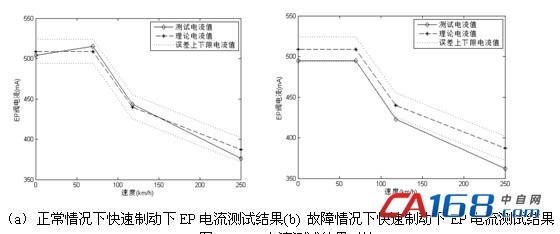
图14 EP电流测试结果对比
在防滑板100V PWM输出特性功能是否正常的测试中,运用PXI 6602板卡,在LabVIEW中配置输出幅值为5V,占空比为23%的PWM,防滑板110V PWM输出波形如图15所示,可知防滑板性能正常,也验证了PXI 6602板卡的输出精度较高,完全满足测试需求。
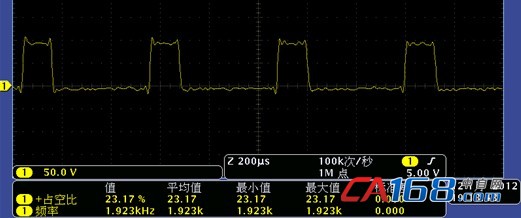
图15 现场测试波形
五、结论
在分析BCU单板测试所需资源的基础上,采用 PXI 系统为硬件测试平台,通过对电路板测试系统的技术需求分析和对测试系统的组成原理的研究,完成了测试系统的硬件设计及系统信号调理板的设计。软件设计方面,采用LabVIEW 软件遵循模块化设计方法,完成了自动测试测试子程序及测试界面的设计,人机交互可视化界面的设计,包括系统启动初始化界面、试验实施界面、手动测试界面,管理主数据界面等。测试人员通过对人机交互界面的操作,可以实现对测试子程序的调用,最终完成对电路板的测试,同时可对测试结果进行保存和打印。实际的测试结果验证了本系统的可行性与可靠性,达到了预期的设计目标。NI公司提供的软硬件产品为我们动车组制动控制单元单板测试试验台的开发提供了高效、便捷和灵活的支持,缩短了开发的周期,受到用户的一致好评。
共0条 [查看全部] 网友评论