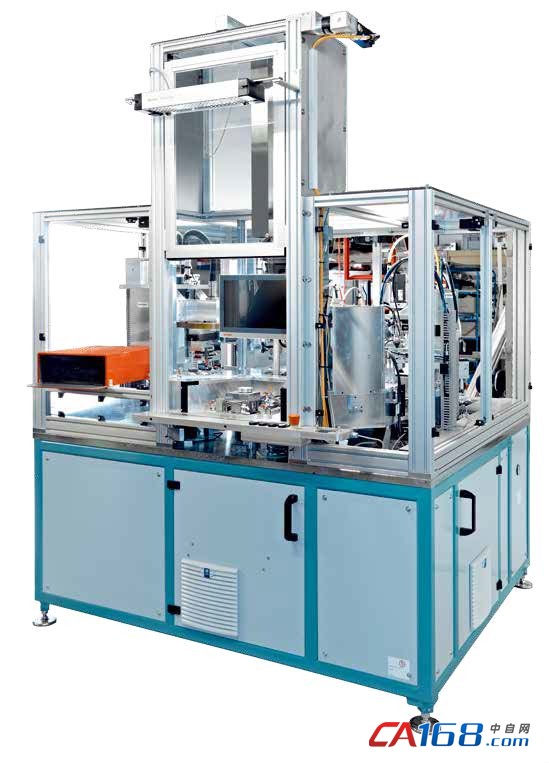
由于采用了基于 PC 的高性能控制技术并集成了高端测量技术,下线测试仪的结构非常紧凑
自动测试设备是一台下线测试仪,用于为驾驶员进行车辆内控制元件的综合测试。驾驶员可以使用这些功能来操作照明设备、收音机、空调导航系统及其它设备。通过按压、推动、倾斜、旋转或触摸可以选择各种车载功能。Borrmann 工程咨询有限公司总经理 Andreas Borrmann 解释道:“测试系统的主要任务是全自动触觉测试。大量传感器测量执行不同开关功能时所涉及到的力量和扭矩。转盘应用通过最多八个独立的操作站实施。”其中,全自动装置是市场上集成度最高的触觉测试装置,采用了非常紧凑的控制和驱动技术。再加上功能特别强大的测量技术,这些功能在提供一个坚固耐用、功能强大的解决方案中发挥了重要作用。Borrmann 继续说道:“过去,我们需要使用专用的测量技术才能同步采集力/路径或扭矩/角度数据,而现在,我们可以使用倍福的标准组件。此外,标准 I/O 端子模块甚至能够从设备同步采集总线报文(如 CAN 或 LIN) 。”一台工业 PC 负责完成八个工位的所有控制和测量任务。每个操作控制元件最多有 450 个测试参数,这并不罕见。转盘循环的典型周期时间为 20 秒,这相当于每年生产 300,000 多套驾驶员控制元件。
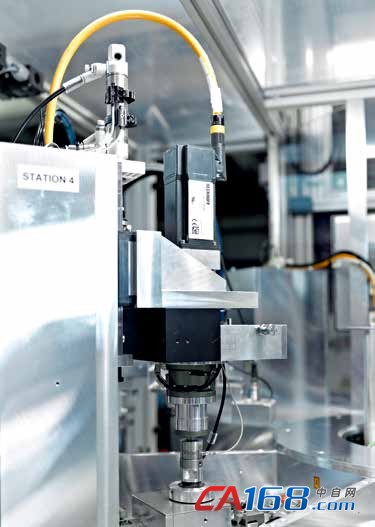
A81xx 系列单电缆伺服电机确保了多达 7 轴的高精度运动
简化复杂测试程序
在测试周期开始时,操作人员主观检查工位 1 中待测试的组件,以检查是否有明显的机械缺陷和表面缺陷,如划痕。一旦将组件放入测试设备,它就会被自动夹紧并与之接触。在设备手动切换和操作人员感观检查确认后,升降机门关闭,转盘周期开始。
LED 指示照明的亮度变化可以超过 30%。在工位 2 中,LED亮度通过摄像机测量的方式进行校准,亮度控制的校正值通过 CAN 报文写入到正在测试的设备的 EEPROM 中。在工位 3 中,使用抽吸夹持器进行剥离强度测试,以确保装饰盖罩被正确胶粘。电感式模拟量传感器检查螺栓是否在,并使用多个传感器确保所有按钮的正确颜色组合。以转矩测量形式出现的第一次触觉测试随后在工位 4 中完成。一个采用压电效应的转矩传感器以最大每秒 180 度的速度旋转,采集分辨率最小为 0.1 Nm 的转矩数据。这一测试的目标是确定开槽以及最小和最大齿槽转矩。齿槽转矩超出所允许的限值表明被测设备在装配过程中出现了故障。Andreas Borrmann 解释道:“我们使用系数为 20 的超采样功能,当任务周期为 1 毫秒时,每秒钟可测量高达 20000 次。因此,每个角度都采集了超过 25 组转矩数据。”
工位 5 专门用于测试车辆压力。在这里也使用了一个高精度的压电式传感器。由于采用了超采样功能,在 10 毫米/秒的速度下可以实现 0.02 N 的力分辨率,位置分辨率为 0.002 毫米。同时,由于任务周期时间只有 1 毫秒,自启动开始就记录 CAN 和 LIN 报文,同时这些报文与运行的位置精确匹配。工位 6 和 7 用到了与工位 5 中相同的测量技术,用于测量水平倾力。
由于倾斜,水平运动中会产生横向力,这些力必须通过精心制作的机械平衡组件来补偿。最后,诸如零件号、序列号、生产日期及其它产品具体信息等数据在工位 8(最后一个工位)中被写入到 EEPROM 中。如果所有测试参数(最多 450 个)的结果都在规定的限制范围内,被测试设备的激光标签通过认证。标签中包含纯文本和二维码(DMC)格式的信息。DMC 阅读器扫描编码并检查内容和质量。在随后的转盘步骤中,经过所有的检查步骤后的模块被输送到工位 1,操作人员在那里将它搬走并打包。
由于倾斜,水平运动中会产生横向力,这些力必须通过精心制作的机械平衡组件来补偿。最后,诸如零件号、序列号、生产日期及其它产品具体信息等数据在工位 8(最后一个工位)中被写入到 EEPROM 中。如果所有测试参数(最多 450 个)的结果都在规定的限制范围内,被测试设备的激光标签通过认证。标签中包含纯文本和二维码(DMC)格式的信息。DMC 阅读器扫描编码并检查内容和质量。在随后的转盘步骤中,经过所有的检查步骤后的模块被输送到工位 1,操作人员在那里将它搬走并打包。
速度和精度都需要 PC 控制解决方案
如果没有倍福基于 PC 的控制技术,下线测试仪的开发几乎是不可能实现的。据 Andreas Borrmann 说:“只有基于 PC 的控制技术才能让我们能够满足测量和驱动技术在速度和精度方面极为严格的要求。由于过去使用的带测量和控制卡的 PC 缺乏可扩展性,现有解决方案在性能上也很有限。而模块化、分布式的倍福技术不再受这种限制,与现有的采用独立测量技术的解决方案相比,硬件成本降低了 70% 之多。”
如果没有倍福基于 PC 的控制技术,下线测试仪的开发几乎是不可能实现的。据 Andreas Borrmann 说:“只有基于 PC 的控制技术才能让我们能够满足测量和驱动技术在速度和精度方面极为严格的要求。由于过去使用的带测量和控制卡的 PC 缺乏可扩展性,现有解决方案在性能上也很有限。而模块化、分布式的倍福技术不再受这种限制,与现有的采用独立测量技术的解决方案相比,硬件成本降低了 70% 之多。”
Andreas Borrmann 看到,整个测量和控制系统可以使用一台工业 PC 集中、方便地控制等更多好处。现有系统中不再需要另外使用 PLC ,由于使用不同制造商的测量技术而涉及到的大量驱动程序安装工作已经成为过去:“集成式系统解决方案在这方面具有显着的优点,例如,基于 PC 的控制还包括高性能、高精度和超高速测量技术。此外,可以轻松地集成车辆内使用的 CAN 协议,以便根据 ISO 15765 标准实现操作元件与控制装置之间的通讯。协议是通过 7 个 CANopen 主站端子模块 EL6751 在 TwinCAT PLC 中建模。与过去使用的技术相比,这样可以节约 80% 的成本。除此之外,现在可以实时地读取和分析 CAN 协议,与被测试设备的全自动同步。以前,这只有使用高度专业化和复杂的电子测量系统才能实现。触觉数据由三个元素组成 — 通过模拟方式采样的力、通过电机直接测定的位置以及通过一个 CANopen 主站端子模块测定的触点 — 现在都可以轻松确定。”
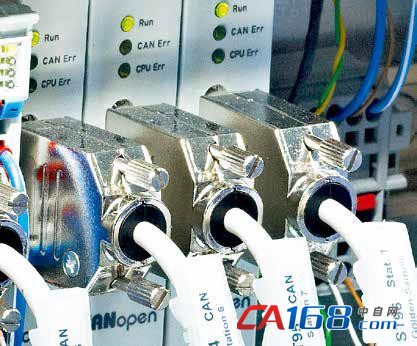
通过 7 个 CANopen 主站端子模块 EL6751 实现与测试设备之间的通讯(符合ISO 15765 标准),与现有的解决方案相比,成本降低了 80%。
具有最小空间需求的伺服驱动技术
Beckhoff的伺服驱动技术也直接集成在 I/O 系统中。各个测试工位中的高精度运动通过 7 根伺服轴组成,每个伺服轴由宽度仅为 24 毫米的 EL7211-0010 伺服驱动模块控制。除了可以驱动额定扭矩为 0.5 Nm 和 0.8 Nm 的 AM812x 系列单电缆伺服电机,这些端子模块还集成了单电缆技术,最大输出电流为 4.5 ARMS。Andreas Borrmann 继续说道:“如果没有以结构非常紧凑的总线端子模块形式出现的伺服驱动器,将不可能实现占地面积如此小的机器。这些产品让我们能够最大限度地减少安装尺寸,且无需使用额外的控制柜。单电缆技术也非常有帮助,因为它在直线和旋转式套管基础上,大大简化了原本复杂的电缆布局。绝对值反馈技术也带来了很大优势,因为它不再需要使用以前所需的参考开关,因此显著降低了驱动技术的复杂性。”
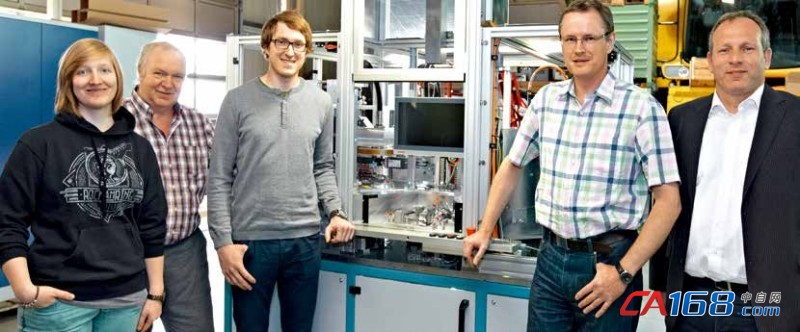
来自 Schuhriemen Maschinenbau 公司的 Jasmin Schuhriemen、总经理 Hans-Julius Schuhriemen 与 Stefan Schuhriemen; Borrmann 工程咨询公司的总经理 Andreas Borrmann;以及来自倍福法兰克福区域办事处的 Jörg-Michael Vetter(从左至右)
倍福的PC 控制结构
– 分布式和集成式测量和控制解决方案降低了 70% 的成本
– CANopen 主站端子模块 EL6751 降低了 80% 的通讯(符合 ISO 15765 标准)成本
– EtherCAT 模拟量输入端子模块 EL3702 确保通过超采样高精度测量压力和转矩
– 伺服电机端子模块 EL7211 和 Am81xx 系列单电缆伺服电机大大降低了空间需求
– 分布式和集成式测量和控制解决方案降低了 70% 的成本
– CANopen 主站端子模块 EL6751 降低了 80% 的通讯(符合 ISO 15765 标准)成本
– EtherCAT 模拟量输入端子模块 EL3702 确保通过超采样高精度测量压力和转矩
– 伺服电机端子模块 EL7211 和 Am81xx 系列单电缆伺服电机大大降低了空间需求
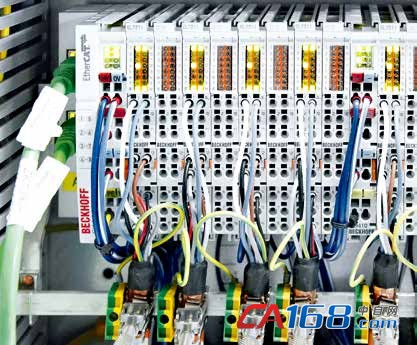
采用了单电缆技术的伺服电机端子模块 EL7211-0010 是实现紧凑型设计和精确运动控制的关键组件
系统集成先进的测量技术
主站端子模块,其余的个数字量输入端子模块个数字量输出端子模块个通道。测量技术通过相应的个超采样系数为通道模拟量输入端子模块个负责完成电流、温度和信号测量任务。数字量万用表端子模块通道电阻测量端子模块
概览
针对汽车行业的解决方案
用于车载控制元件的下线测试装置
为客户带来的好处
最小化的机器占地面积和集成经济高效的测量技术
共0条 [查看全部] 网友评论