1 控制系统的选用及系统的硬件配置
1.1 控制系统选用及应用要求
碳酸二苯酯装置自动化控制系统采用艾默生公司的具有工厂管控网结构体系的控制系统,该系统基于FF 总线技术,采用标准的开放式协议进行操作,可以与企业内已联网的全部智能现场设备进行交互,更重要的是它的规模可变性,这一优势提供未来系统进一步改扩建的灵活性及充分利用原有的控制系统设备,节省工程费用。以下是利用该系统特点提出的设计要求:
(1)考虑到系统的可靠性和安全性,由 DCS 控制器承担主要的过程控制计算,所有的复杂控制算法都由 DCS 控制器完成,现场总线设备不参与控制及计算。
(2)充分利用系统规模可变性特点,在控制网络里安装两台专用应用站,安装 OPC 服务器、设备管理系统服务器等应用软件,且互为冗余。安装两台远程DCS 操作站,满足用户在现场进行系统的操作、监控与维护等工作。
(3) 借助于管控网结构良好的开放特性,安全系统(SIS)和 DCS 系统之间的通信采用基于 Modbus 的TCP / IP 的通信方式,这种方式可以把 ESD 控制器通过交换机和任意多个 DCS控制器之间信息共享,利用网络中的核心交换机引入 GPS 时间,实现 DCS 和 ESD系统的时间同步。
(4) 尽可能使用总线智能设备,如智能执行机构,马达控制器等,对于测量仪表,非安全相关的仪表设备必须选用 FF 智能仪表,安全相关的模拟量仪表设备必须选用带 HART 通信功能的智能仪表,开关量信号采用 NAMUR 类型,变频和非变频马达控制器选用 Profibus DP 通信协议的智能设备。
(5) 为确保控制系统的安全性和高可靠性,必须对以下关键部位实行冗余设计:
·控制系统柜、网络柜的电源采用相互独立的两路 UPS 供电系统 1:1 冗余设计;
·控制器(CPU)卡件和通信卡件采用 1:1 冗余设计;
·连接机架间的数据线冗余设计;
·控制系统间的控制通信网络、交换机等通信设备冗余,冗余的通信电缆一路走装置的电缆桥架,一路走地下通信用的电缆井。采用冗余配置的设备有故障时系统会实现自动无扰动的切换,并发送相应的报警信息。
1.2 控制系统硬件配置
控制系统包括 DCS 控制站 18 个,新增 DCS 控制站采用 MX 控制器,原有控制站的控制器升级为 MX控制器;ESD 控制站 8 个,新增 ESD 控制站采用 Hi-max;服务器 5 台,包括 2 台应用站,2 台远程操作站,1台专家站;操作站 4 台,工程师站 2 台。I/O 点数如表1 所示。
项目执行过程中要对控制器的主要技术参数进行测试和计算,每个控制器的各项参数设计要求:空余内存 >35%;空余存储器 > 30%;DST 的备用点 > 20%;每个控制站备用 I/O 通道 >20%。
表 1 I/O 点表
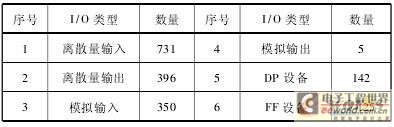

2 改造后控制系统的架构设计及功能描述
2.1 控制网络架构的设计
基于现场智能设备的工厂管控网是一种规模可变的开放式结构体系,方便系统扩容及原有资源的利用。考虑到对现有系统资源的充分利用,降低控制网络和生产网络的工程费用。项目只对控制网络进行扩展,对于新增远程操作站及 I/O 站,通过光纤接入新机柜室的冗余控制网络柜的主副网上实现远距离的控制。新机柜室的控制站通过以太网线连接至冗余通信柜,再通过光纤远距离传输至原有通信柜的主副控制网络中,实现与控制室网络,生产网及办公网络的连通。新增操作站、服务器直接接入现有控制网的主副网中,以实现对工厂生产的控制操作和工艺信息、报警信息的监测。
利用现有系统的生产网、办公网,构建一个工艺控制自动化、仪表设备智能化、企业管理信息化的现代化工厂,系统架构如图 1 所示。
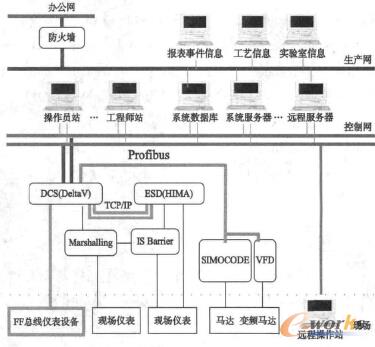

图 1 碳酸二苯酯装置控制系统架构
2.2 功能描述
(1)智能现场设备层
主要分为三种类型智能设备、测量仪表:FF、Profi-bus 及 HART 协议类型的变送器、执行机构、马达控制器等现场智能设备,这些设备通过现场总线与相应的智能 I/O 通信卡件接入控制系统,构成工厂管控网的第一层。
(2) 控制网络层
由图中结构看出,控制网络中 DCS 系统是工艺生产流程的过程控制核心,实现对各种复杂工艺过程的控制、工艺和系统报警信息的监测等。安全系统是独立的子系统,其通过 Modbus TCP/IP 接入 DCS,实现信息的共享、互为操作。操作站和工程师站作为操作和日常维护的界面。
(3) 生产网络层
通过 OPC 协议,将控制网上的生产信息、设备信息、操作信息等集成起来,实现对现场设备进行远程巡检和诊断,对工艺操作信息、报警历史数据等进行存储监控和分析。
(4) 办公网络层
生产网经过防火墙与办公网共享生产信息和集团网络连接实现集团内信息共享,实现设备维修管理信息、生产数据、库存管理等生产资源的调配和管控一体化。
3 现场总线设备在装置中的应用及项目设计要求
基于工厂管控网技术的 DeltaV 系统能够很好地兼容来自各种现场总线设备。本装置的智能控制设备如马达、变频马达控制器全部采用 Profibus DP 设备,智能传感器、变送器等测量仪表、阀门执行机构则采用FF 现场总线,对于涉及到安全系统的仪表,则全部采用 HART 协议仪表。以下是项目中的 FF 现场总线设备和 DP 设备的特点及设计应用要求。
3.1 基金会现场总线的应用与设计基础
在碳酸二苯酯装置改造扩建项目中,对现场总线设备的选用有明确的要求,必须是经过测试的证实个体故障发生时对整个段内的其他设备无影响。该项目采用的 FF 现场总线设备主要有萨姆森(SAMSON)智能执行机构、E + H(Endress + Hauser)、西门子(Sie-mens)、威卡(WIKA)、泰科(TYCO)等供应商的压力、液位、温度、流量变送器,FF 现场总线网段共 220 个,平均每个网段挂 5. 3 台 FF 总线设备。在 FF 现场总线设计、组态过程中,严格遵守如下规定:
(1)现场总线最大允许长度与电缆类型、网段的拓扑结构及本质安全要求等因素有关。本项目中 FF现场总线的通信速率采用 31. 25 kbit/s,现场总线电缆采用 18 AWG(A 型)屏蔽电缆,相应的性能参数见表 2。该类型的总线电缆在没有中继器时的最大总长度为 1 900 m,分支电缆的长度为 30 ~ 120 m。每个Segment 现场总线电缆总长度是所有支线电缆长度的总和加上干线电缆长度。每个 Segment 现场总线电缆总长度要依据总线供电设备的容量,是否采用本安回路、网段总的功率负载、线上压降等进行计算。尽量降低通信负荷,FF 现场总线网段的设计必须满足:每个非本安网段(Segment)挂设备数量不超过 8;每个本安网段挂接设备不超过 4 个;其中执行机构最多 2 个,在没有变送器的网段上可挂接 3 个执行机构;每个网段上保留 20%的备用量;同一回路的测量、执行器放在同一网段内。
表 2 现场总线电缆性能参数表
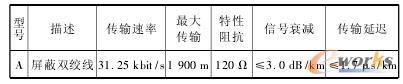

(2) 现场总线设备如果安装在 I 区,总线供电电源要采用有安全栅功能的接线盒。总线可以直接给连接在该总线上的低功耗总线设备供电,但是对于一些高功耗的总线设备则需要采用单独的供电回路。
对于连接在本安现场总线需要总线供电的总线设备,考虑到本质安全总线上供电电流的有限性,在设计中要采用低功耗的现场总线设备。
需要采用单独供电的总线回路中的供电设备要采用特殊的防爆措施进行有效地隔离,以保证外部供电电源和总线设备所连接的通信回路完全隔离。外部电源的能量在任何情况下都不允许转移到本安总线上,以确保单独供电设备和总线上的所有现场总线设备在危险区的安全使用。
(3) 网段拓朴结构,项目设计中现场总线设备的现场安装位置按所属单元分布比较集中,适合采用树形拓扑结构。树型拓扑网络结构是由多个智能设备与公共接线箱连接的多条独立现场总线支线组合而成的结构,支线电缆只能从公共接线盒中即干线电缆引出,不能从其他支线电缆引出,以确保总线的可靠性要求。总线电缆的连接要保证支线电缆的屏蔽线绝缘一定要做好,各段总线的干线电缆的屏蔽线必须在机柜侧的接地端子上接地,电缆对地绝缘良好,这一点对 FF 总线设备的正常使用非常重要;另外,在接线盒的各分支上增加防短路保护功能以确保通信信号不受干扰。树型拓朴结构如图 2 所示。
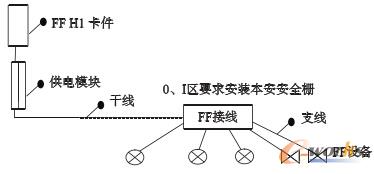

图 2 树型拓朴结构
3.2 Profibus DP 总线的应用及设计基础
项目中所有的转动设备控制均采用 SIEMENS 的Profibus DP 总线智能设备 SIMOCODE 马达控制器和VFD - G120、VFD - G150 变频马达控制器,这种方案大大地增强了 DCS 对现场马达控制的操作与监控,在
项目设计时,主要遵循以下几点要求:
(1) 现场马达的控制设备采用的 SIMOCODE 控制模块安装在马达控制中心(MCC)的机柜内,每一个MCC 机柜都设计一个 DP 中继器和一排终端集线器,在每个段上的最后一个总线设备都安装终端电阻,根据 DP 设备网络图,同一个网段上的 MCC 机柜通过中继器连接到一起,与本网段上的 DP 通信卡连接。每个 MCC 柜内的中继器用来分开子网段,当一个子网段发生故障时不会影响同一个 DP 卡上的其他的子网段。
(2) DCS 对马达控制信号如启动/停止信号、变频器的转速信号及转速设定值、马达的运行信号、电流过载及其他故障信号、功率信号等都由 Profibus 通信实现。但对于由 DCS 紧急停止马达的控制,则由 DCS的 DO 输出,通过硬接线到 MCC 柜实现。
(3) 依据设计要求,现场要求安装启动/停止操作柱及远程和就地选择开关,当开关拨到就地控制时,马达启动只能在现场启动,当拨至远程控制位时,由DCS 启动。而停止马达不受开关位置限制,就地和DCS 都可以在任何时候停止马达的运行,该方案大大提高了马达控制的灵活性和安全性。通过编程,可以实现 DCS 远程自动启动马达,而当出现紧急故障时,根据当时的情况既可以通过现场操作柱也可以通过DCS 发出停止马达命令。
(4)DP 数据传输速率设置为 500 kbit / s,在不使用中继器的情况下一个网段的最大传输距离是400 m。在通信过程中阻抗不连续和阻抗不匹配都会导致信号反射,导致通信质量和通信距离的降低。为了消除在通信电缆中的信号反射,确保总线上的设备无差错的运行,必须确保接线质量,严格设置每个物理网段中的各个节点设备的终端电阻,如图3,网段中间站点的终端电阻要打到 OFF 位置,网段两头的终端电阻要打到ON 的位置。
3.3 HART 协议智能仪表的应用及设计基础
项目对于 HART 智能设备的应用,主要满足于安全仪表系统的要求,由于安全系统对测量仪表的安全性和可靠性要求高,需要对每个回路进行 SIL 等级的计算。项目中采用满足 SIL 等级要求的 HART协议测量仪表,在传输 4 ~ 20 mA 的信号上叠加了HART 协议的数字信号进行双向数字通信,数据传输率为 1. 2 Mbit/s,采用双绞同轴电缆最大传输距离可达 1 500 m。这样既满足安全系统接收 4 ~ 20 mA 的模拟 信 号 的 需 要,又 借 助 于 PlantWeb 组 件 中 的HART 技术,将 HART 设备中的丰富过程参数信息传送至 DCS 内嵌的资产管理系统中,实现设备的诊断和管理功能。对于 HART 协议仪表测量设备,主要考虑以下几点:
图 3 DP 设备连接及终端电阻图
(1) 每个 HART 仪表都通过一个分配器将信号分成两路,一路 4 ~20 mA 信号接到 ESD 系统,一路接到 DCS,由 DCS 采集 HART 信号。
(2) 如果现场来的信号需要接入 DCS、ESD 系统外的其他子系统,需要串接两个分配器则第一个分配器的输出接入 DCS,以避免叠加在模拟信号上的数字信号失真。
4 结束语
本项目利用基于现场总线的工厂管控网结构的自控系统,成功实现了碳酸二苯酯厂 20 万吨/年到 40 万吨/年的改扩建工程,并将工程的工期由原计划的 28个月缩减为 25 个月,这其中重要的原因之一就是项目采用基于现场总线技术的自控系统方案,这一方案的应用,很明显缩短工程自控设备的安装调试时间,使得工程得以提前开工试运行,为节省人工成本和缩短项目周期发挥了重要作用,为其他类似的工厂构建一个工艺控制自动化、仪表设备智能化、企业管理信息化的现代化工厂提供参考。
共0条 [查看全部] 网友评论