所以在最近几年里,更多的牙膏厂商采用了智能视觉系统用以检测灌装生产线。现今,慧眼公司特制了一套视觉系统用于每分钟生产450支牙膏的自动灌装生产线,检测内容包括:
(1)灌装前,检测牙膏管是否干净;
(2)灌装前,管形圆度是否合格;
(3)灌装后,密封性是否良好、色标是否对中等等。
设备运行运行过程中,一个配备有扩展钳爪的6轴机器人将管筒从装运的箱子中取出,并且将它们放进传送带系统的管筒支架中,使得管筒的始终保持开口端朝上。机器臂装配有一个特殊工具,该工具有多个夹脚,精确对应箱子中的每个分格,并且可以一次性取出两排共30支的管筒。螺丝盖子已经在管筒的顶部安装到位,管筒的下端开口以便于填装。传送带系统以顺时针方向将管筒移动到清洁和填装站。在它们到达清洁和填装站之前,使用一台扫描仪检查是否已经正确对齐,这样就可以保证后期密封基部时印刷的位置正确无误。随后的两个检查站点在管筒进入清洁和填装阶段之前确认管筒在形状上是圆形并且是洁净的。
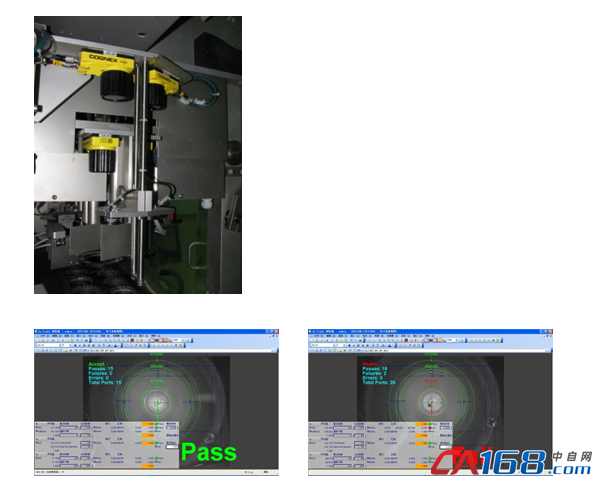
1、 管形检测。在随后的管形检查过程中,安装在传送机和工作区域上方的智能相机2对管筒的尾部进行拍照料检测。系统选用一个红色低角度环形光源从四周把牙膏管尾是否认边缘照亮,使整个圆形的轮廓显现出来,再用BLOB、圆度判断等算法对产品进行检测。
3、 密封性检测。在清洁和填装之后,使用热气来密封夹层塑料管筒。管筒的末端采用温度为380到450°C的热气进行加热,然后由冷却的冲压钳压在一起。密封采用光滑压纹或者采用波纹压纹,并且可以压印序列号或者代码。在包装过程的这一阶段中可能发生缺陷:例如,如果某刀片变钝,不能正确地切除管筒的末端,密封的边线就会很粗糙。因此在修整站,使用相机3对产品进行最终拍照检测。系统采用白色条形光源,把产品的尾部照亮,再用灰度、边缘等算法,对产品进行检测,把尾部未密封好的、色标未对中的产品剔除出来。
整个检测系统已联网到中央面板计算机上,能够自动记录所有的NG图像、数据信息。这使得操作人员无需从生产线上找到剔除出来的实际包装物品,就能够直接通过网络迅速地找到生产缺陷的图片,并快速对工艺进行调节,避免了大批量的次品浪费。
使用了高集成度的智能相机,精简了整个全自动的流水生产线,把繁琐的检测难题变成了所见即所得的检测方法,比传统的生产线要求另外单独人工检查更加可靠,而且效率也提高了好几倍,减少了整体成本。
共0条 [查看全部] 网友评论